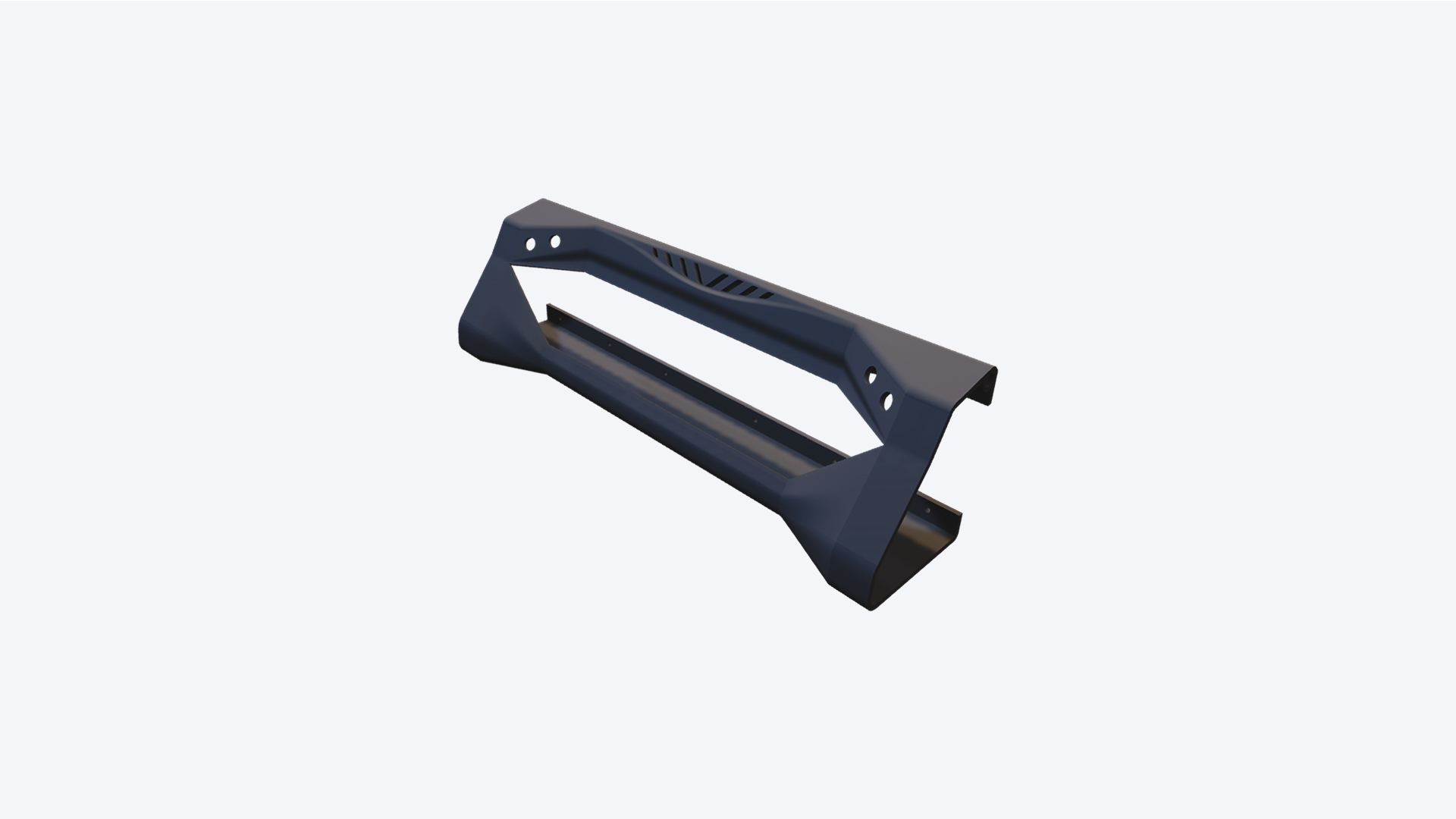
Super polimeri e produzione additiva di parti di largo formato: come cambia la produzione ferroviaria
Il settore ferroviario sta attraversando una trasformazione epocale grazie all'adozione di super polimeri e soluzioni di produzione additiva industriale per la creazione di parti di largo formato. In questo articolo, esploreremo il contesto di questa innovazione, i vantaggi che comporta e presenteremo un caso di studio, esposto in anteprima mondiale durante il Formnext 2023, relativo a un pannello customizzato all'interno della carrozza di guida di un treno.
Interni Ferroviari: sfide e opportunità tra standardizzazione e personalizzazione
Nel contesto attuale della produzione di interni ferroviari, l'attenzione si concentra su diversi aspetti, tra cui design ergonomico, sicurezza, comfort e materiali durevoli. Le parti interne delle carrozze ferroviarie sono spesso realizzate con materiali tradizionali come legno, acciaio inossidabile, plastica rinforzata con vetro (GRP), e altri, resistenti alla propagazione del fuoco in caso di incendi. Questi materiali sono selezionati per garantire robustezza, durabilità e facilità di manutenzione.
Nei processi tradizionali la produzione di interni impiega principalmente il metodo dello stampaggio a iniezione per parti in polimero e il taglio e la saldatura per le parti in metallo. Questi metodi, sebbene consolidati, possono comportare limitazioni in termini di complessità del design e tempi di produzione. Gli interni delle carrozze ferroviarie, infatti, spesso seguono design standardizzati per garantire uniformità e conformità agli standard di sicurezza. Questo approccio può limitare la personalizzazione e l'adattabilità delle soluzioni alle esigenze specifiche dei clienti.
Inoltre, negli ultimi anni, c'è stata una crescente attenzione all'integrazione di tecnologie di comfort, come sistemi di intrattenimento a bordo, prese di corrente e illuminazione regolabile. Tuttavia, l'integrazione di queste tecnologie spesso richiede modifiche significative agli interni esistenti.
I limiti descritti possono essere affrontati con nuovi approcci come l’uso di super polimeri, come PEKK e ULTEM 9085, e la produzione additiva sbloccando nuove opportunità nella produzione di interni più leggeri, resistenti e personalizzati. Questi materiali offrono anche certificazioni dedicate al settore ferroviario. Ne sono degli esempi il PEKK, certificato UL94 V0, l’ULTEM 9085, certificato EN45545, o il ToolingX CF, intrinsecamente auto-estinguente e classificato V0 secondo la norma UL94. Inoltre, è certificato per il settore ferroviario R22 (HL1) e R23 (HL1 – HL2 -HL3) secondo norma EN 4554-2. L'integrazione di queste tecnologie può ridefinire il panorama della produzione di interni ferroviari, offrendo soluzioni più avanzate, efficienti e sostenibili. Vediamo come.
Vantaggi della produzione additiva industriale di parti in super polimero di largo formato
La produzione additiva di parti in super polimero di largo formato emerge come una prospettiva rivoluzionaria, offrendo una serie di vantaggi significativi che ridefiniscono i paradigmi della progettazione e della produzione. Tra i più rilevanti citiamo:
1. Leggerezza e resistenza: I super polimeri offrono una combinazione unica di leggerezza e resistenza, permettendo la creazione di parti più leggere senza compromettere la robustezza strutturale. La leggerezza del materiale, inoltre, contribuisce anche a una riduzione del consumo di carburante, rendendo l'intero sistema più efficiente dal punto di vista energetico.
2. Personalizzazione: La produzione additiva consente la personalizzazione delle parti in base alle specifiche esigenze. Questa flessibilità è cruciale per adattare le soluzioni alle varie configurazioni dei treni e alle esigenze particolari dei clienti.
3. Riduzione dei tempi di produzione: Utilizzando processi di stampa 3D avanzati, è possibile ridurre significativamente i tempi di produzione rispetto ai metodi tradizionali. Ciò consente una maggiore efficienza nella catena di approvvigionamento.
4. Sostenibilità ambientale: La produzione additiva riduce gli sprechi di materiale, contribuendo a un approccio più sostenibile alla produzione industriale.
Il caso del pannello ferroviario customizzato realizzato con ARGO 1000 HYPERMELT
Immaginiamo di dover sostituire un pannello critico nella carrozza di guida di un treno. Utilizzando la produzione additiva industriale e il materiale ULTEM 9085, tra i polimeri ad alte prestazioni con certificazione FST (flame, smoke, toxicity), è possibile progettare e fabbricare un pannello su misura che soddisfi esattamente le specifiche richieste. La personalizzazione non compromette la resistenza e non comporta alcun costo aggiuntivo. Inoltre, grazie alla stampa 3D industriale, il pannello può essere realizzato in tempi record, riducendo al minimo i tempi di fermo del treno per manutenzione.
Una volta ottenuta la parte col metodo additivo, si procede a tecniche di post-processing come la sabbiatura e la verniciatura, per ottenere la rugosità e la finitura estetica-funzionale desiderate. L’ultimo step è la validazione della parte finita, cruciale per verificare dettagliatamente che il componente rispetti tutte le specifiche richieste. Questo può includere ispezioni visive, test di resistenza, analisi dimensionali e, se necessario, test di conformità agli standard di sicurezza FST.
Il paradigma tecnologico di HYPERMELT
La tecnologia HYPERMELT equipaggiata sulla soluzione ARGO 1000, è un nuovo paradigma nel campo della produzione additiva di polimeri ad alte prestazioni, basato sull'utilizzo di pellet come materia prima. Questo approccio innovativo consente la produzione di parti di grande formato con un'ampia gamma di materiali avanzati, tra cui super polimeri come PEKK e ULTEM 9085, compositi come PEEK e PA caricati con fibra di carbonio, elastomeri, materiali riciclati e polimeri a base biologica. La tecnologia HYPERMELT rappresenta una svolta nell'uso della stampa 3D nella produzione.
Superando i limiti dei volumi di stampa 3D tradizionali, la tecnologia HYPERMELT è in grado di produrre parti con una velocità di produzione 10 volte superiore e costi ridotti fino al 60% rispetto ai metodi a filamento, mantenendo un'elevata precisione di deposizione rispetto alla stampa 3D a pellet di grande formato (LFAM) già presente sul mercato.
ARGO 1000 HYPERMELT è il risultato del lavoro di alcuni dei migliori ingegneri e scienziati dei materiali del mondo. Hanno lavorato anni per sviluppare quello che speriamo diventi lo strumento utilizzato dai migliori innovatori e inventori del mondo per cambiare la produzione. Se ti consideri uno di loro, contattaci oggi stesso, esplora le potenzialità di ARGO 1000 HYPERMELT e unisciti a noi nel plasmare il futuro della produzione. La tua creatività e visione possono essere la chiave per spingere i confini dell'innovazione industriale.