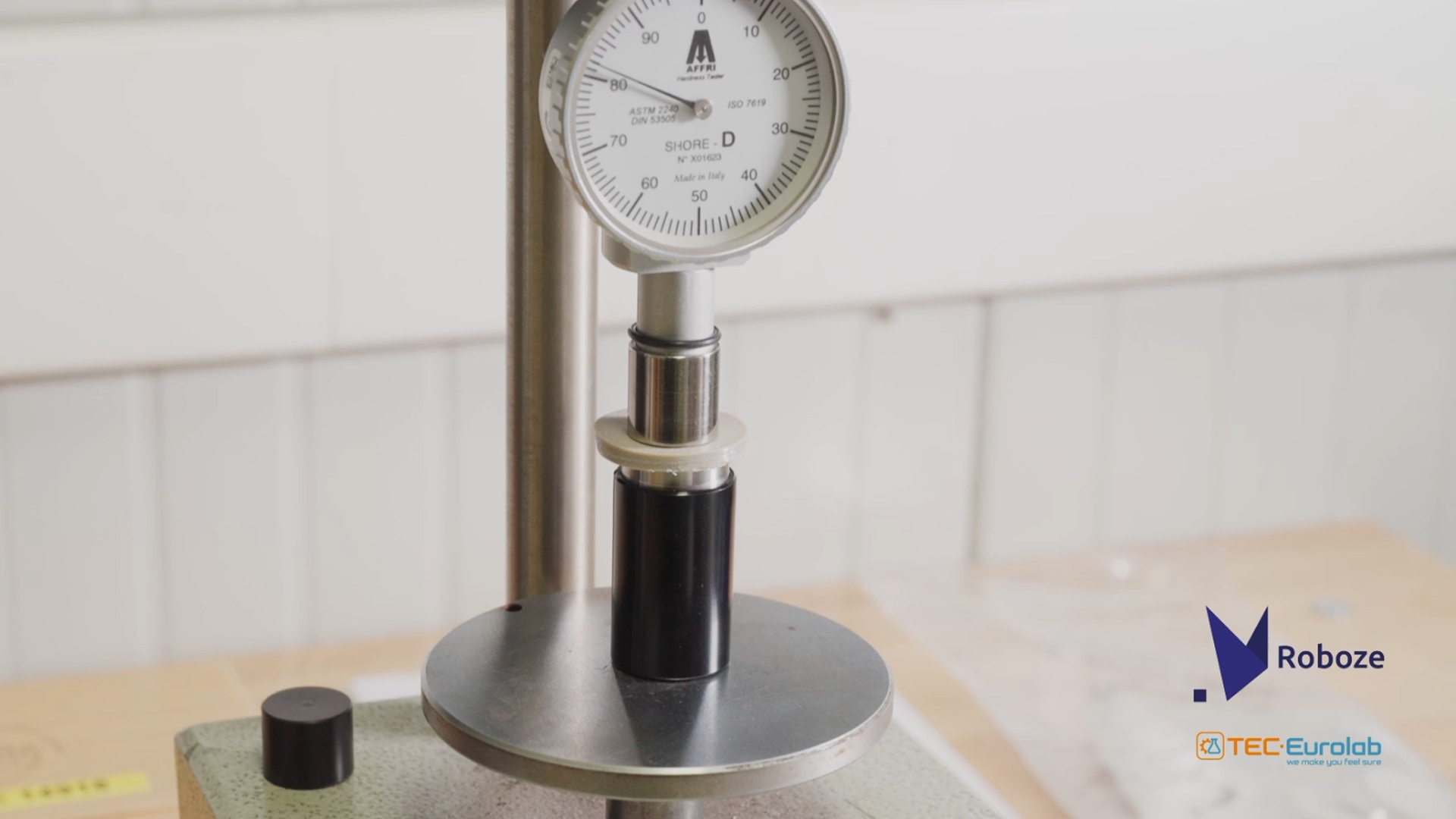
PEEK is often chosen for applications that require a high resistance to surface wear, often in the presence of a compressive load. In addition to high mechanical loads, high temperatures and chemically aggressive environments, functional components can also be subject to wear when used. The latter is generally caused by surfaces in metal, ceramic or polymeric material that move with relative motion to each other with respect to the surface of the component under analysis.
PEEK test: the measurement of the Shore D hardness
PEEK’s properties such as the material's excellent creep resistance, low thermal expansion coefficient, self-lubricating properties, low coefficient of friction, high compressive strength, and the ability to maintain mechanical properties at elevated temperatures make this material ideal for the production of plain bearings, thrust washers, sealing rings, bushings, etc. However, the study of tribological processes is complex due to the multitude of operational factors that come into play:
- type of coupled surfaces;
- macro and micro-geometry of the surface;
- behavior of the third body;
- sliding speed;
- contact pressure;
- operating temperature.
One of the quickest and simplest PEEK tests that allows us to provide information on the tribological behavior of a polymeric material is the measurement of the Shore D hardness.
What is the hardness of materials?
Hardness is defined as the resistance that a material opposes in being deformed in a plastic and permanent way, by a specific indenter forced to penetrate through the surface of the material to be analyzed. Hardness is inversely related to the ease of penetration but directly related to the elastic modulus value and the viscous behavior of the material.
A polymeric material with a high Shore D hardness value will have excellent properties of mechanical strength, resistance to wear, abrasion, and scratching.
The hardness test to characterize Roboze PEEK
The hardness test, used to characterize the behavior of PEEK, was performed in accordance with the ASTM D2240 standard, in collaboration with TEC Eurolab, an accredited third-party laboratory - specializing in the characterization of materials and non-destructive testing, training and certification. For hard plastic materials, such as PEEK, the shore D scale is used.
How do we measure hardness values?
The test method involves pressing a tapered indenter on the surface of the material with a given force and for a given time frame. The hardness value is read while the indenter is in contact with the test sample.
Before carrying out a measurement, a calibration check of the instrument is performed with specific reference samples, choosing the standard with a shore D hardness that can be correlated to that expected from the test sample. This verification is performed with the same test conditions (load and application time) used for the test on the material to be analyzed.

Production process of PEEK specimens
As for the tensile test, the production requirements of the PEEK specimens analyzed are:
- Chamber temperature = 160°C;
- Extrusion temperature = 470°C;
- Printing speed = 1800 mm/min;
- Layer height = 0,22 mm;
- Infill percentage = 100%;
- N.2 shells.
The specimens used are cylindrical geometry samples with a diameter of 30 mm and a thickness of 6 mm printed with the base lying in the XY plane ("flat" configuration) and raster angle equal to ± 45 °.
The measurements are performed using an analogic durometer Affri 3002 Shore D.
PEEK hardness test: results
The test procedure requires the specimen to be placed on a hard flat surface, where an indenter penetrates it while maintaining parallelism with the surface. Finally, the hardness is read within a certain time, in the case of this test is equal to 1s of contact with the specimen. The measurements are performed 3 times on the same sample and the result is therefore the average value of these measurements.
Shore D hardness | ASTM D2240 | 84 |
The data analysis shows a perfect concordance between the empirical values and the data present in the literature for conventional production technologies. In fact, PEEK made using Injection Molding technology returns a hardness value of 85 ShD, only 1.2% higher than that measured for a sample made using additive manufacturing technology.
If you want to know more and access all the mechanical, chemical, and thermal tests, carried out on the Roboze PEEK material, download the TDS in the dedicated web page.