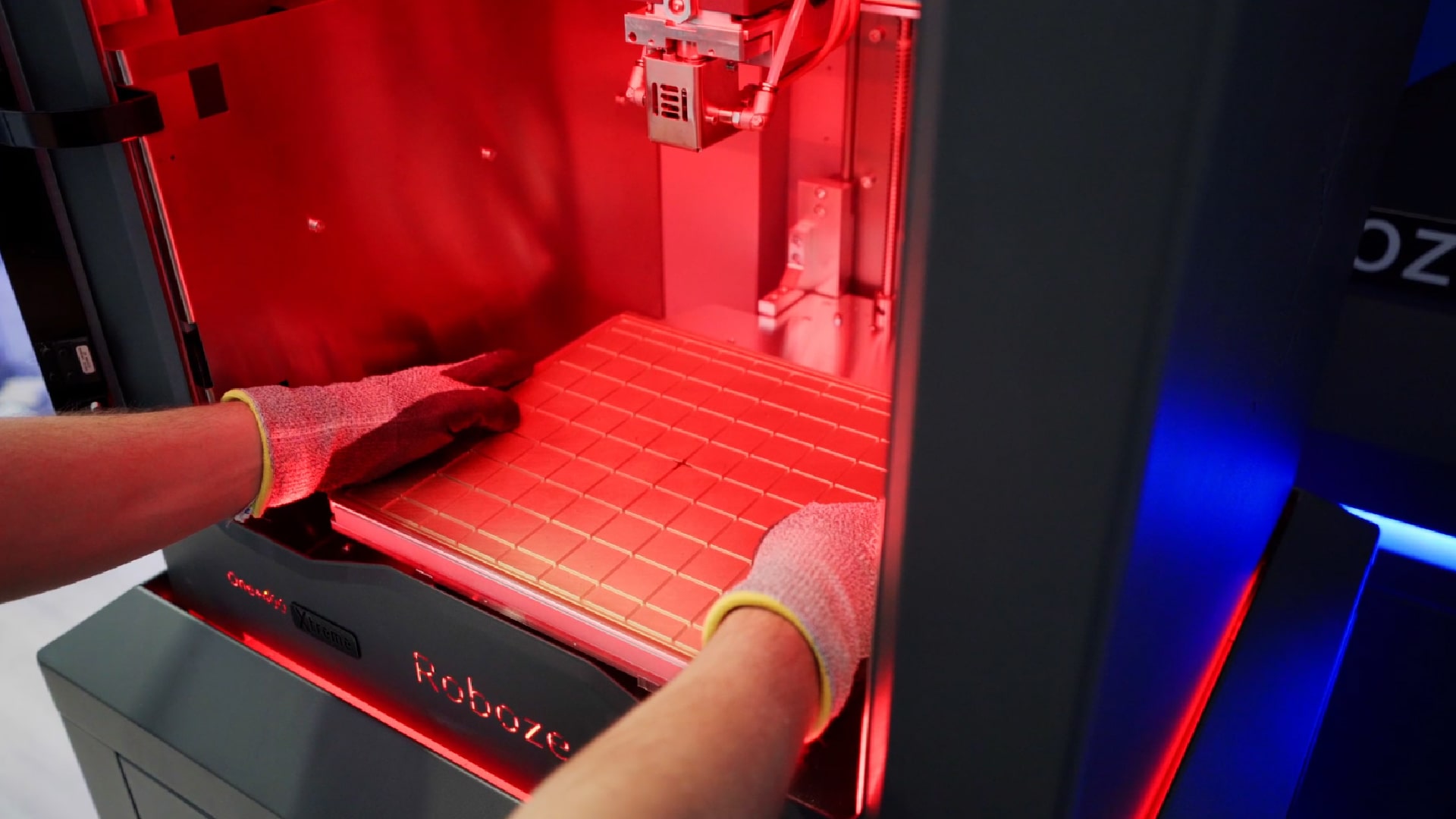
Why should you also consider set-up times when choosing a 3D printing solution?
During 3D printing processes, very often the term efficiency is accompanied by that of speed. In additive manufacturing it is common to pay close attention to the speed variable associated with the printing time of the part at hand. However, in order to have true efficiency in the production process, it is necessary to keep in mind different variables that guarantee productivity and the economy of the process in its entirety, in addition to quality and compliance with technical specifications.
To achieve this goal, the preparation phase becomes strategic and acquires great importance for control before and during printing.
How to reduce setting-up times: advantages of Roboze Xtreme series
The solutions of the Xtreme series, consisting of the Roboze One Xtreme and Roboze One + 400 Xtreme, provide a very low set-up time compared to competitor solutions as they have been developed considering this strategic phase. All the elements that contribute to achieving this goal are described below.
Beltless System
Like every Roboze machine, the Xtreme series is characterized by the presence of the Beltless System, the direct mechatronic movement system of the axes that has removed belts from 3D printing. The adoption of helical pinions and racks, on the one hand, guarantees a mechanical positioning accuracy of 15 μm, and on the other, it allows support of printing speeds of up to 4000 mm / min. Unlike systems equipped with belts, maintenance operations consist of the simple application of a thin layer of grease once a month, with several advantages:
- significant reduction of machine downtime;
- no calibration loss over time;
- no belt tensioning;
- same production process for years to come.
Filament drying and self-loading system
The Xtreme series machines are equipped with a material drying system, the Roboze HT Dryer. It is a galvanized steel device designed to dry the filaments and preserve their properties in a stable and reliable way during the entire production process: from conditioning to the end of printing. Active drying allows constant humidity control in the filament for weeks, while the perfect integration of the device into the printer enables it to automatically load and unload logics that lead to a quick and standardized process, never influenced by the operator.
Automatic calibration of the Z-axis
Xtreme solutions minimize manual operations. The automatic calibration of the Z-axis (patent pending) automatically sets the correct distance between the print bed and the extruder, compensating for any tolerance chains related to the wear of the film or the installed extruder. This reduces the operator's manual operations, creating a faster process which is more reliable and perfectly repeatable over time.
Vacuum System
When working with super-polymers, having optimal adhesion of the first print layer is essential. Instead of glass plates or micro-perforated surfaces where you must apply vinyl glue or lacquer, the Roboze systems use specific polymeric film sheets for each filament which are held on the surface of the print bed by the vacuum system. This solution speeds up and simplifies the commissioning operations, reducing set-up times and increasing the efficiency of the device.
This series is ideal for the production of functional equipment and components with the possibility of using techno polymers that ensure excellent performance, such as PEEK, Carbon PEEK, and Carbon PA. To learn more, do not hesitate to contact us at info@roboze.com or directly from our dedicated page.