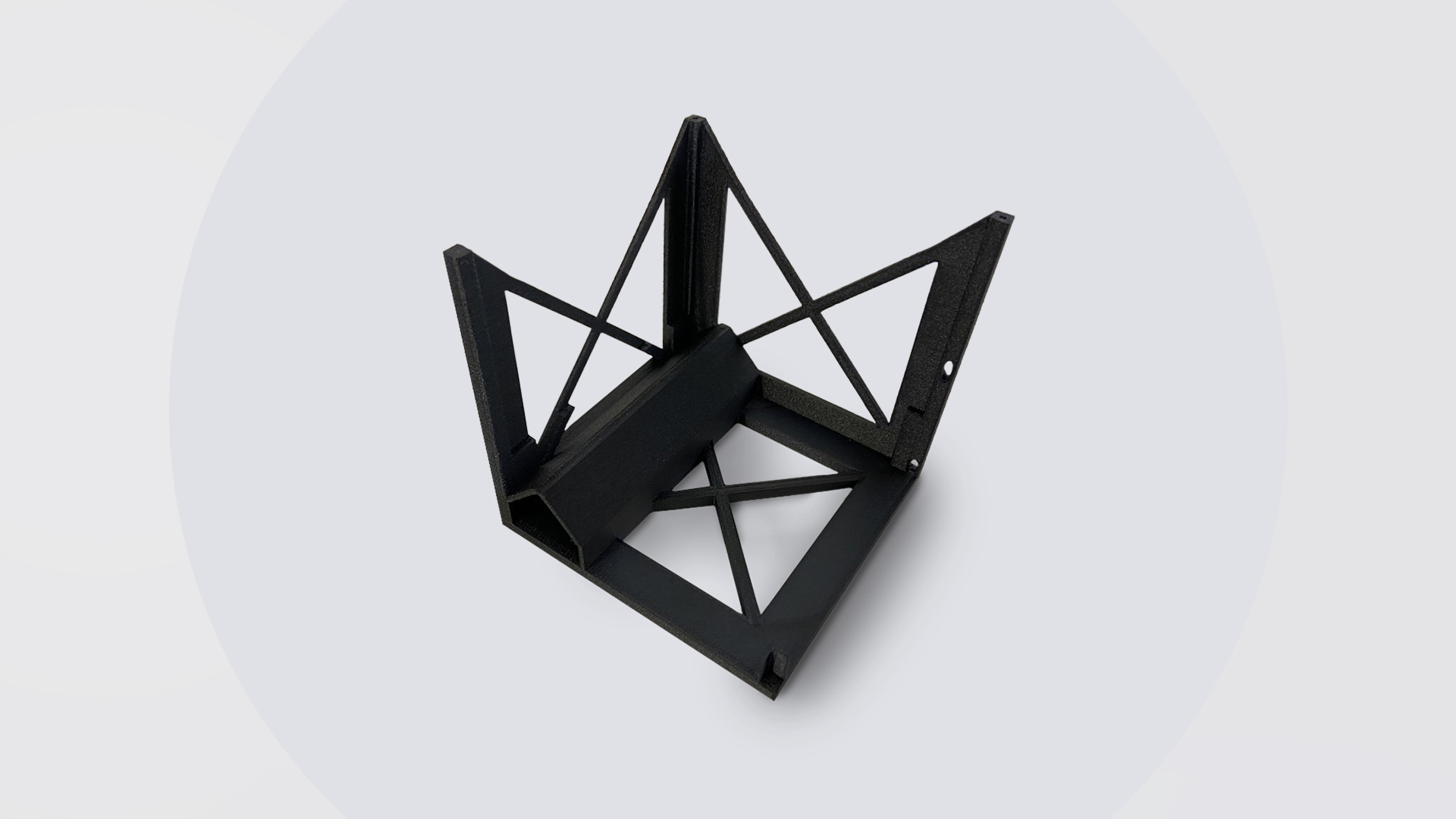
The potential of additive manufacturing in the space sector
The space sector is constantly looking for solutions to improve the efficiency of the structures of its spaceships and produce parts with complex geometries. In recent years, organizations such as NASA, ESA and SpaceX have conducted numerous characterizations in order to better understand the potential of additive manufacturing and hypothesize new production methods.
Although it is essential that the parts and components used are first of all reliable and certified, the economic investment and the required quality standards are also significantly relevant.
Generally, the components for space applications are produced through traditional methods with a consequent limitation in the geometries of the parts and substantial costs linked to timing and low production volumes.
Roboze additive manufacturing: amazing performances
Additive manufacturing opens up new opportunities to the sector with a significant reduction in weight thanks to the construction method that increases the complexity of objects right from the design stage, and thanks to new materials replacing metals with lower densities, offering a potential improvement of performance and a consequent reduction in the fuel required. All this translates into a reduction in the costs required to get rid of the gravitational attraction of the earth and the costs of process and procurement.
The system temperature is one of the factors that affects the fuel efficiency of jet engines, in fact an increase in temperature corresponds proportionally to an increase in consumption. 3D printing allows the construction of engines with more efficient cooling systems, reducing the temperature of the combustion chamber and therefore the amount of fuel used.
Roboze 3D printing in the space sector: advantages and opportunities
Roboze 3D printing allows you to design parts with high performance materials such as CARBON PEEK, PEEK or ULTEM ™ AM9085F:
- CARBON PEEK is a composite material reinforced with carbon fiber, with the most extraordinary characteristics in terms of mechanical, thermal and chemical resistance. The addition of carbon fiber makes the PEEK matrix even more resistant from a mechanical point of view and allows you to go further in the Metal Replacement process even in the most extreme industrial sectors such as Space. Used in a wide range of industrial sectors, Carbon PEEK is chosen in very specific areas where a further increase in mechanical performance is required compared to PEEK.
Below you can see a Cubesat, a miniaturized satellite used in the space sector and in research, made with Roboze's CARBON PEEK material. The part incorporates a fuel tank with an outlet pipe, holes for the passage of cables, and has been designed to be printed without supports, reducing printing time and cost.
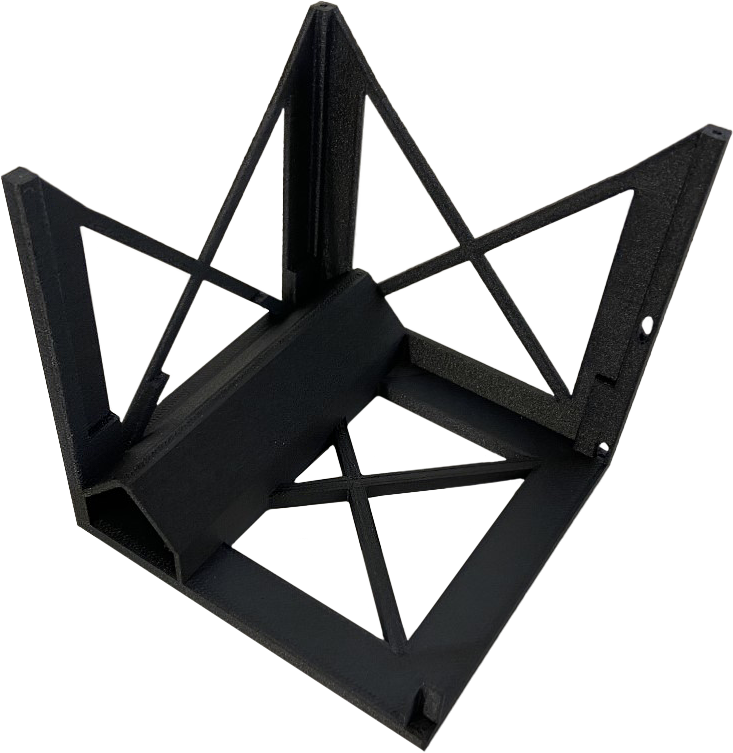
- PEEK is a semi-crystalline thermoplastic, certified by “Outgassing ECSS QST70” which guarantees shielding properties of the outgassing of materials for the manufacture of spacecraft and associated equipment. The thermal vacuum test establishes the critical design parameters, temperature and pressure; and the acceptance criteria.
- ULTEM ™ AM9085F is an amorphous polymer, known for its particular self-extinguishing ability. The UL 94-VO and FST (flame, smoke and toxicity) certification certifies the high resistance to the development of flames and the non-toxicity of the fumes developed during its combustion. It could therefore be used for parts located outside spacecrafts, subject to high doses of radiation and extreme temperature changes.
3D printing allows you to:
- Design by exploring the various possible design alternatives in order to bring advantages in terms of filling the part while ensuring the necessary resistance to be able to use it correctly;
- Use alternative materials to allow greater lightness rather than particular mechanical resistance, heat or chemical agents;
- Optimize the layout with complex geometric shapes by eliminating unnecessary parts, minimizing the amount of material used.
Further advantages of 3D printing can also derive from the automation of processes: one of the most frequently encountered problems in the production of missiles and satellites is the actual impossibility of making small series of batches or prototypes without incurring high production costs. Roboze 3D printing systems play a fundamental role in this context since the resulting advantages are concrete and immediate.
You can produce parts by choosing to implement Roboze solutions directly in your processes or choose to make them On Demand and Just in Time with the support of the 3D Parts network, specialized centers distributed around the world that use the Roboze Production platforms for the realization of parts with high quality standards wherever and whenever you want.
If you want to know all the advantages offered by Roboze in the production of parts for the space sector, contact one of our consultants: info@roboze.com
#PrintStrongLikeMetal #OnDemand