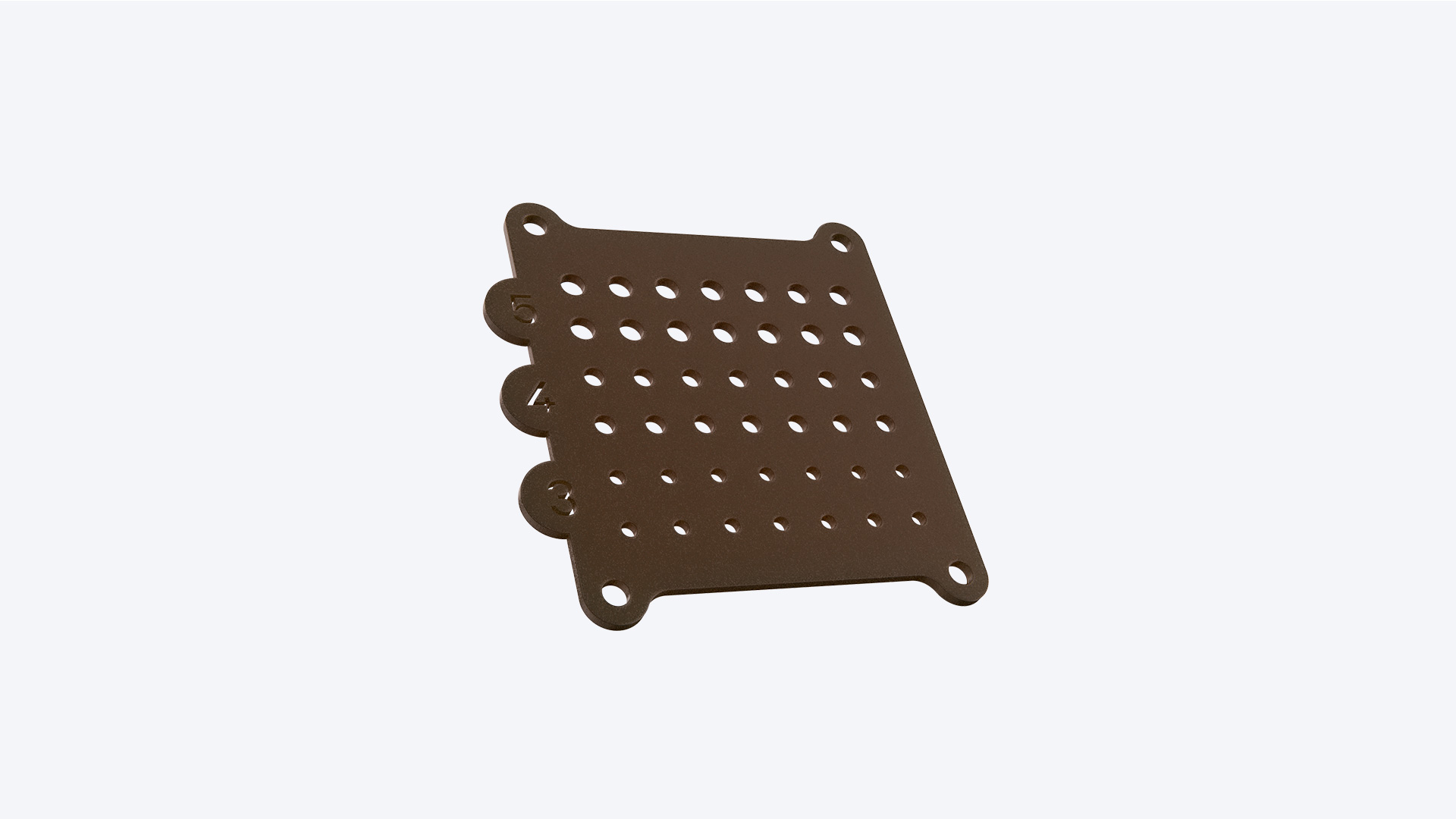
Take Control of Your Tooling: High-Performance In-House Production
At the heart of every industrial process, efficiency often depends on elements that may seem secondary: jigs, fixtures, and support tools. These components don’t end up in the final product, but they are essential to ensuring quality, speed, and safety during production. Traditionally, creating them involves long wait times, supplier lead times, and intensive CNC machining. In today’s fast-paced environment, where rapid response is a competitive edge, that model is no longer sustainable.
Today, thanks to additive manufacturing with high-performance thermoplastic materials, it’s possible to produce tooling directly in-house, with greater autonomy, control, and speed.
A new production strategy
Reducing setup times and increasing CNC availability are two critical objectives for managers of complex production environments. Outsourcing tooling can slow down the entire workflow, creating bottlenecks and external dependencies. By contrast, in-house production allows teams to respond more quickly and precisely to design changes, urgent production needs, and unexpected events on the shop floor.
Additive manufacturing fits into this context as a practical, industrial solution. It’s not just a new technology, it’s a new way of thinking. Companies can dramatically cut down tooling lead times, reducing delivery from weeks to just a few days, or even a few hours in some cases.
Performance and operational freedom
Producing tooling internally means no longer waiting for supplier confirmations, no minimum order quantities, and the freedom to iterate quickly during design. It also opens the door to materials that can withstand mechanical and thermal stress, making additively manufactured tools not just faster to produce, but reliable in real-world industrial applications.
These tools can be tailored to the exact needs of your production team, with complex geometries, lightweight structures, or integrated functions that would be difficult, or too expensive, to achieve using traditional methods. This level of customization directly enhances operational efficiency and process quality.
Supporting industrial transformation
Bringing tooling production in-house is a key step in the shift toward leaner, more digitized production models. It’s a way for companies to regain control of their own processes, making them more responsive and less exposed to external constraints.
It’s also an opportunity to free up resources, reduce outsourcing costs, and make more efficient use of CNC systems by reserving them for high-value and mission-critical parts.
Companies choosing this path aren’t just adopting a new technology—they’re transforming how they operate. They’re choosing control.
Ready to bring technical tooling production in-house?
With Roboze solutions, you can integrate a reliable, high-precision system into your shop floor, compatible with the most advanced materials and designed to help you save time, costs, and dependencies.
Talk to the Roboze team and explore the opportunities for your production line.