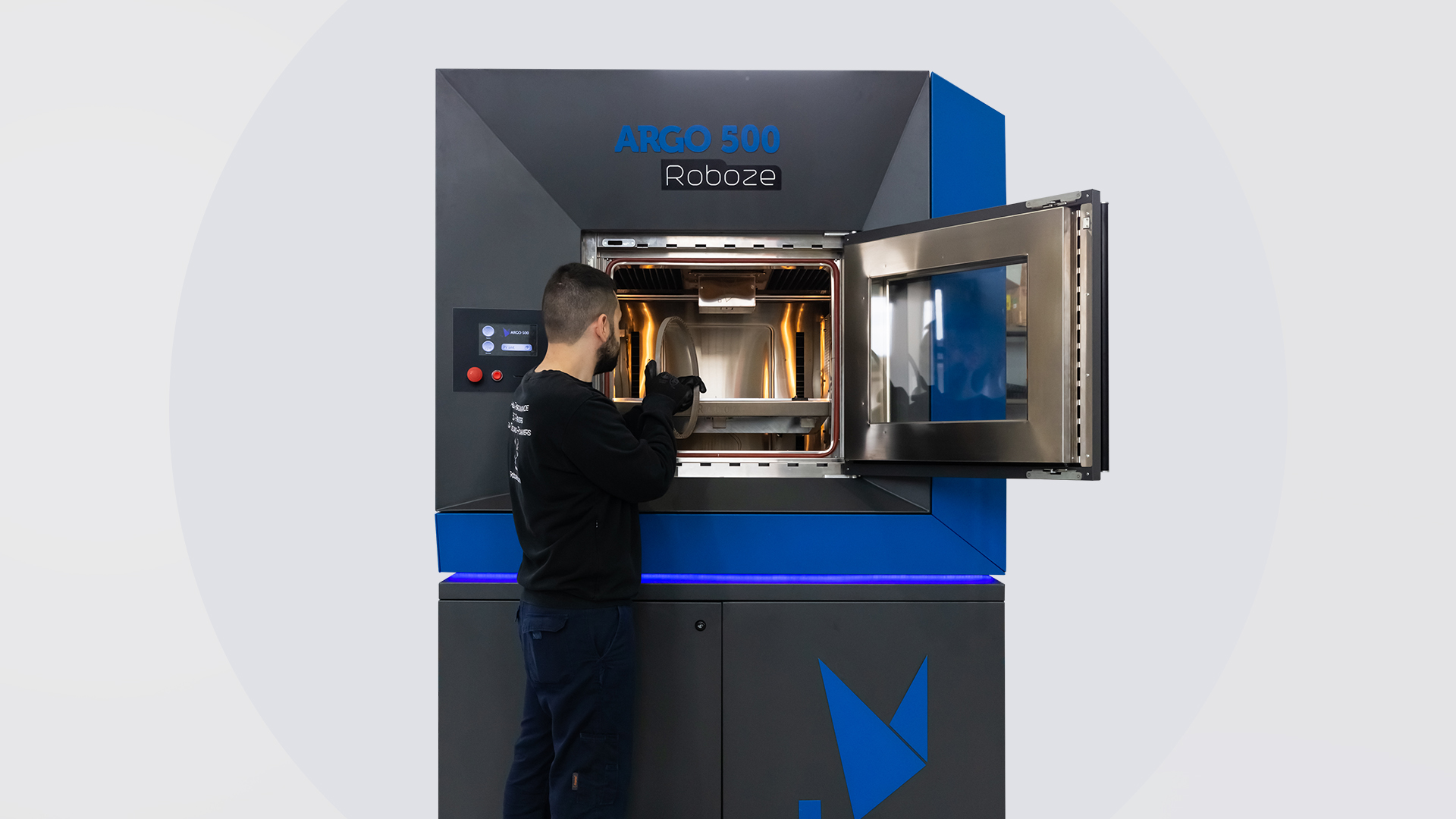
ROBOZE 3D printing technology and the manufacturing future
Additive Manufacturing in the industrial sectors: how are the manufacturing processes changing?
Additive manufacturing is changing the way products are realized in several industrial sectors. According to Wohlers Report 2019, those companies that have introduced 3D printing systems within their manufacturing processes for the realization of functional prototypes and finished parts represent the 56.3% of the total.
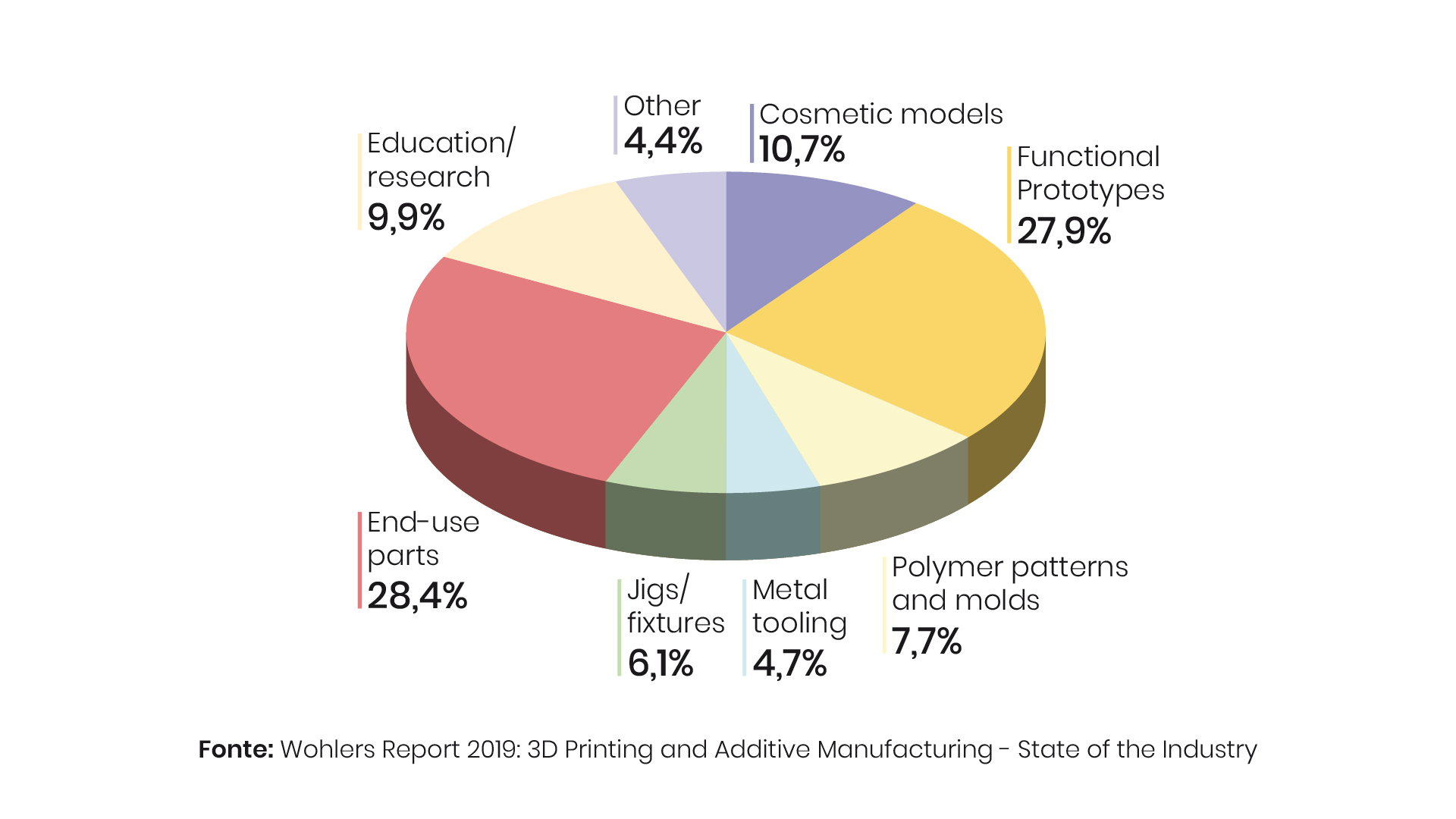
The introduction of additive manufacturing within the traditional production processes allows a company to reduce the lead-time of a product and better control the quality and the cost of the components in its manufacturing line. Additive manufacturing guarantees also more freedom in terms of design and possibility to create components that could not be easily realized with traditional manufacturing because of too long production time and extremely high costs.
Advantages and uses of Addictive Manufacturing
Using super polymers and composite materials instead of metals is advantageous for industries like Aerospace, Motorsport, Oil&Gas and Automotive thanks to the possibility to reduce the weights of the parts and get more chemical resistance to the corrosion and more workability of the plastics compared to metal alloys.
In the FFF 3D printing market, Carbon PEEK is the material with the greatest properties for extreme applications. The addition of carbon fiber makes the PEEK matrix even more resistant in terms of mechanics and allows to go further in the Metal Replacement process in Motorsport, Oil&Gas, Aeronautics and Aerospace industries.
The evolution of the market and the industrial developments in the 3D printing era
The industrial sector is therefore witnessing a real revolution, driven by the continuous evolution of additive manufacturing. For companies like Roboze, it is extremely important to invest time and resources in R&D, in order to get aligned with the rapid changes of the market worldwide. More and more often, especially in US and Asia, the manufacturing industries use both 3D printing and traditional methods with CNC machines.
In particular, additive manufacturing is changing the future of the aerospace and defense sectors: here the biggest challenge is reducing the weights of the aircrafts with lighter parts, keeping high the performance standard of the produced components. Roboze 3D printing technology – for examples thanks to PEEK, the semi-crystalline thermoplastic polymer that guarantees the most extreme performance with its mechanical properties and the excellent thermal and chemical resistance – allows the companies working in these sectors to replace light alloys like aluminium with super polymers, guaranteeing the reduction of weights, fuel consumption and CO2 emissions.
Education and technological know-how, with a good knowledge of printers, materials and post-processing techniques are, therefore, fundamental for this industrial revolution driven by additive manufacturing, that, together with Roboze, aims at supporting customers in getting the best advantages from this great opportunity offered by 3D printing.
Contact Roboze experts for a personalized consultancy and get ready to print strong like metal.
Email at info@roboze.com
#PrintStrongLikeMetal