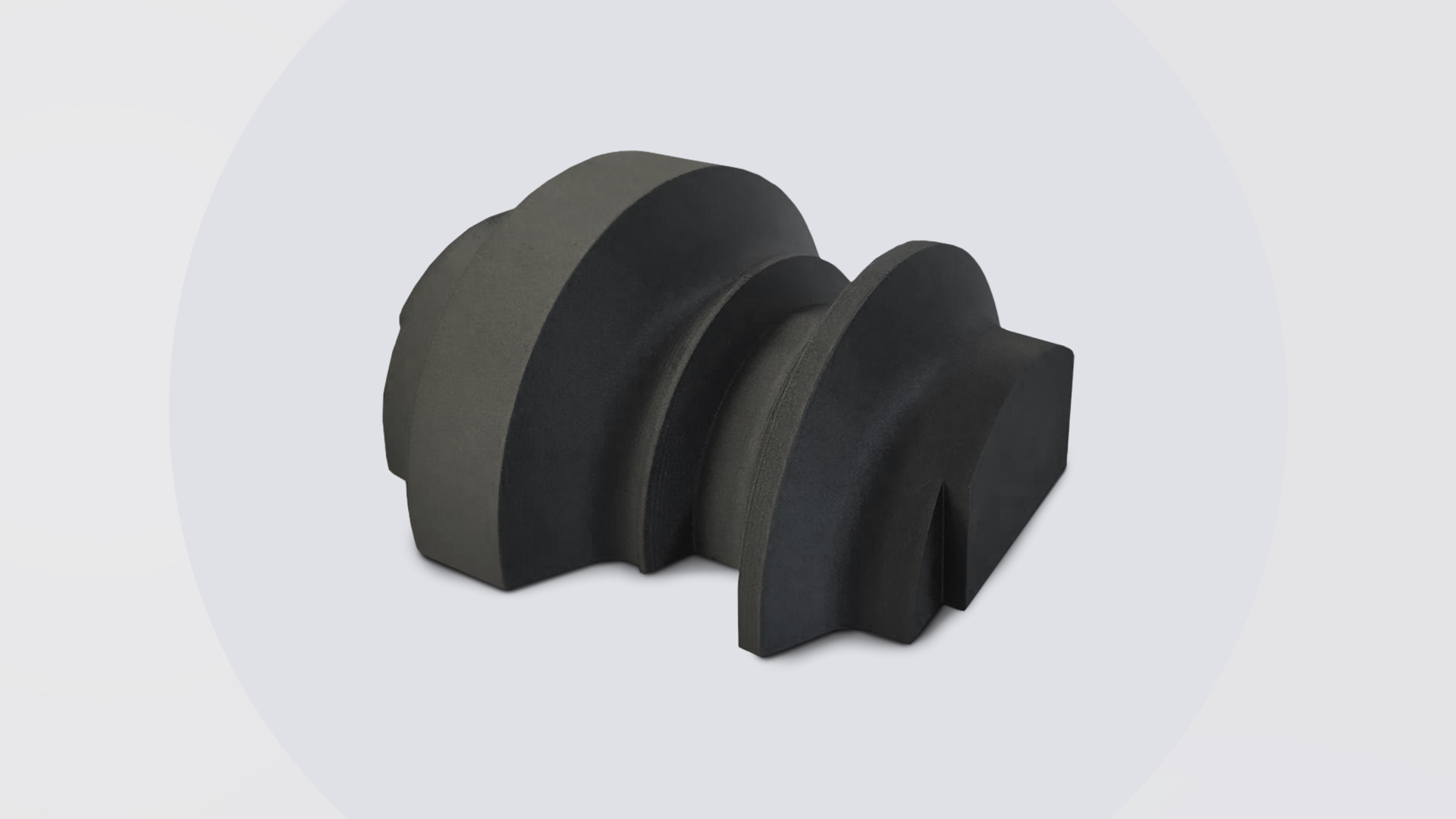
Roboze 3D printing solutions: the role of additive manufacturing in the production of moulds
Rapid and versatile solutions for applications in the foundry sector
The production of objects by fused metals casting in special moulds, is one of the oldest known forming processes, with origins dating back to 4000 BC.
The industrial development we have witnessed in recent years, increasingly inclined to rapid prototyping and mass customization, has also exerted an important influence on foundries, which have to deal with the demand for small production batches in a short time.
In this evolutionary process, additive manufacturing plays a key role, proposing a rapid and versatile solution for the production of functional parts with complex geometries, capable of reducing time to market and keeping production costs low.
3D printing solutions are used in various processes of lost patterns casting, whose mould, used for the creation of the piece, is destroyed at the end of the job.
These procedures can include permanent patterns or lost patterns. The former ones include techniques such as sand casting; among the latter ones, lost wax or investment casting.
Roboze Carbon PA for sand casting
The sand casting is a versatile and cheap process, used for both mass production and small batches production, with weights ranging from few grams to several tons.
The casting technique mainly consists in preparing a cavity, called mould, within a bracket in soil or sand, that contains a negative impression of the intended shape. The fused metal alloy is poured into the mould.
Once the alloy has solidified, the mould is broken to allow the extraction of the casting, very similar to the final piece, except for the allowances needed on the functional sides.
The patterns are usually made of wood, resin or metal and can also consist of multiple parts (cores) when passages and cavities are expected in the finished product.
The use of 3D printing for the realization of the patterns allows to reduce the time and costs associated with the production of tooling, enabling the production of partially hollow parts with complex or custom geometries.
Furthermore, the properties of Roboze composites allow to properly manage the temperatures and compression forces involved during the sand molding phase, guaranteeing a resistance to wear that gives the chance to create more shapes with the same pattern.
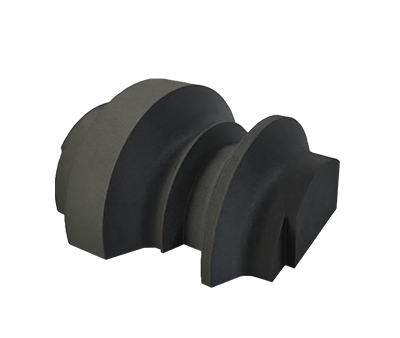
Roboze Ultra for investment casting
The investment casting is an industrial casting process, valued for its ability to produce semi-finished shapes, that requires little subsequent processing.
The traditional process starts from the realization of lost patterns, usually obtained by die-casting of the wax inside a mould specially built in aluminum alloy.
Once the patterns are welded forming the so-called “cluster”, this is immersed in a ceramic mixture (slurry) and then in a refractory mixture.
Once ready, the structure is heated until the wax melts, leaving a cavity ready to receive the fused metal.
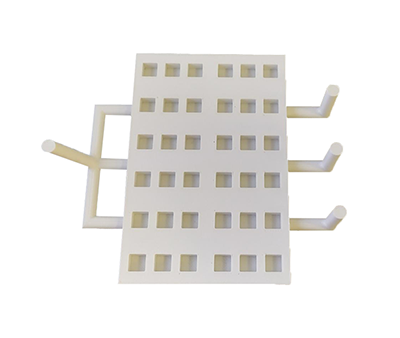
The use of 3D printing for the direct realization of the lost pattern allows you to avoid having to stock up on aluminum moulds into which to inject the wax, eliminating any logistics and warehouse problems.
Furthermore, by internalizing the production process, it is possible to reduce the associated times, from 3-4 weeks to 2-3 days, with considerable money savings.
The filament chosen for these applications is Ultra - PLA, a polymer that is easy to print and which allows for an excellent surface finish in a fine tolerance class. The parts produced are usually characterized by a low filling (% infill), which allows to further reduce production times and material used.
Discover how to accelerate these processes in your company, get in touch with us.