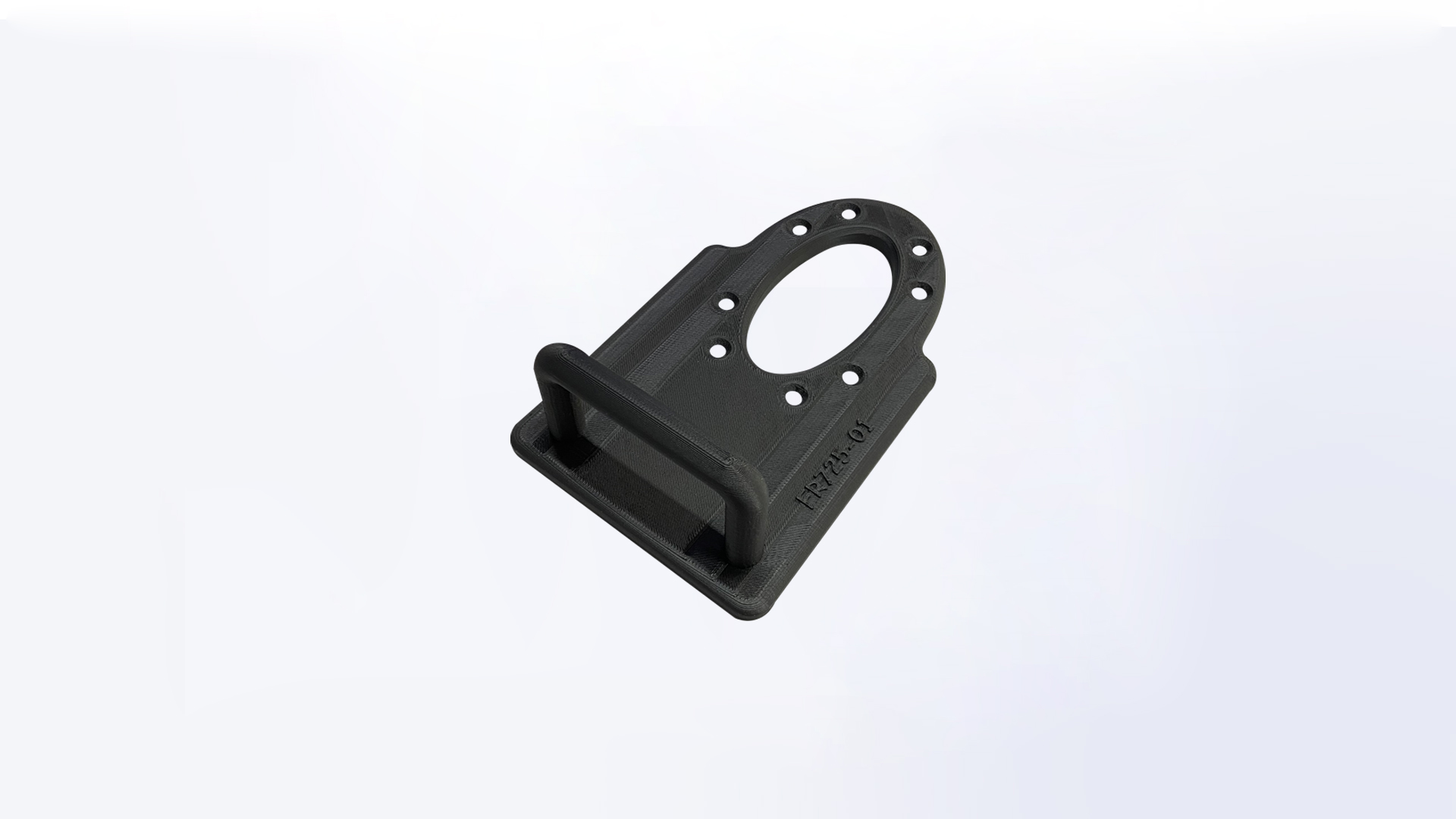
What are Pitot tubes and what are they used for?
The Pitot tube, also called Pitot probe, was invented in the 18th century by Henri Pitot and refined in the 19th century by Henry Darci: to this day is widely used in many sectors to measure the speed of fluids. Pitot tubes have many applications, for example on boats to measure the water speed, in aircraft to measure the airspeed, and in industry.
The focus of this article is on the 3D printing solutions offered for the aviation industry, where Pitot tubes provide vital information to pilots in the form of the aircraft’s true airspeed, which is simply the speed at which an aircraft is moving relative to the air it is flying in. In simple terms, airspeed determines whether an aircraft can fly, as opposed to ground speed which determines how long it takes to reach its destination.
The two are different when there is wind, which will modify the speed at which the air moves around the wings. For example, if the aircraft has a tailwind, its ground speed will be higher than its airspeed. The reverse is true in the case of a headwind.
Pitot tube construction and installation
Pitot tubes are typically part of an aircraft’s system called the Pitot-static system, which is used to measure the airspeed, Mach number, altitude, and vertical speed. Aircraft usually have between one and two Pitot tubes which are located on the wings or towards the front of the aircraft, facing forward, where they are exposed to the relative wind.

A Pitot tube is installed in the selected location by drilling a hole of the correct shape in the wing or body of the aircraft; the probe itself is then bolted to the aircraft to prevent it from moving.
The problem with Pitot probe installation: the drilling
Different aircraft models and configurations have Pitot tubes in different locations: this can be problematic since aircraft have round surfaces so drilling holes on aircraft with the right shape is difficult and ad-hoc jigs are sometimes built. The correct alignment of the Pitot tube depends on the shape of the hole and the location of the screw holes, so it is very important for the drilling jig to have the correct geometry.
Production of a Pitot tube drilling jig with Roboze 3D printing
Additive manufacturing has the unique advantage of a level of design freedom that is unparalleled, compared to traditional manufacturing. Therefore, printing an ad-hoc jig to guide the drilling of the hole for the installation of Pitot tubes is very easy. Roboze produces the most accurate and repeatable fused filament fabrication (FFF) printers on the market, allowing the quick 3D manufacturing of high-quality jigs for the installation of Pitot tubes.
But all the advantages of 3D printing are for naught unless combined with a high-performance material that can withstand the drilling process: Carbon PA PRO is a perfect candidate, a composite of Nylon and short carbon fibres that elevates the virgin plastic to new heights.
An example 3D printed drilling jig on a Roboze ARGO 500 using Carbon PA PRO is shown in the picture below:
- The surface is slightly curved to better position the tool on the fuselage and to allow better alignment;
- The tool is designed to be held with one hand while the other operates the drill;
- Holes have been included in the tool for easy drilling;
- It is very light so can be handled safely and easily by the operator;
- It is also wear resistant, easily handling the vibrations and temperatures caused by the drilling tools.

Material | Carbon PA PRO |
---|---|
Weight | 0.15 kg |
Cost | 30 EUR |
Time | 3 h |
In Roboze we know how important the tooling phase is, which is not simply a tool but describes the design of the tools necessary for production. With Roboze‘s 3D Production solutions, obtaining 3D finished parts that meet the quality and specifications required, in the volumes and delivery times required, at competitive costs, is now a solid reality.
Contact one of our experts for a personalized consultancy.