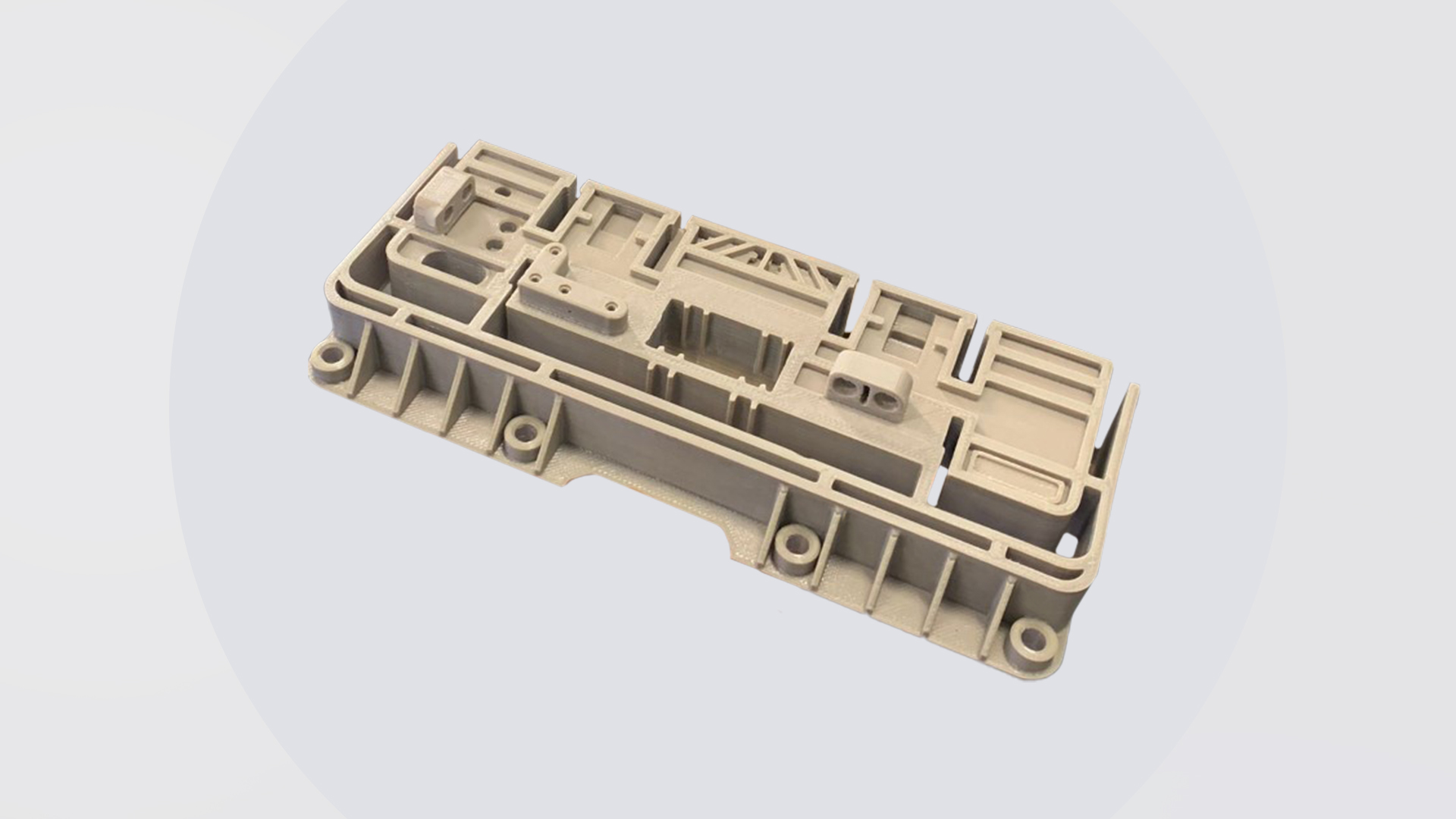
PEEK 3D printing: what is PEEK and what is it used for?
What is PEEK?
Polyetheretherketone (PEEK) is a semi-crystalline, high-performance organic thermoplastic polymer that belongs to the PAEK family. What does PEEK mean?
Let’s look into it.
Is PEEK a Polymer?
PEEK (Polyetheretherketone) is a colourless organic thermoplastic polymer, even though when printed it looks beige-brown (in its Carbon reinforced version, it looks black). Polymers are substances or materials consisting of macromolecules composed of many repeating subunits, called monomers. The molecular strength of the repeating monomers of two ether groups and a ketone group that compose PEEK, provide it of outstanding properties. The high thermal stability of PEEK is provided by the diphenylene ketone groups, which impart also high strength and high resistance to oxidation. Flexibility in the polymer backbone is provided by ether linkages.
Here are some PEEK polymer's chemical properties:
- Is PEEK an Organic Compounds?
In chemistry, organic compounds are generally any chemical compounds that contain carbon-hydrogen bonds. Almost all the plastic compounds used today are organic, constituted of very big molecules made by long chains of carbon atoms. For instance, Polyethilene (PE) is an organic polymer with every carbon atom bonded with two hydrogen atoms.
- PAEK polymer family
PEEK belongs to the PAEK polymer family (polyaryletherketones polymer family) that includes PEK, PEEK, PEEKK, PEKK, PEKEKK and more. The PAEK family is characterized by high-temperature stability and high mechanical strength. Among the members, PEEK is the most widely used 3d printing material and it is manufactured in large scale, also because it is easy to machine, thanks to its metals like behaviour.
Polymers that are thermoplastic become malleable or mouldable at a certain high temperature and solidify when cooling. When higher temperatures weaken the polymer chains, the thermoplastic becomes a viscous liquid that can be easily reshaped and processed with different production techniques like injection moulding, compression moulding, and extrusion.
Polyester (PL) along with nylon (PA) and polyvinyl chloride (PVC) are among well-known thermoplastic polymers.
PEEK changes its state from glassy to viscoelastic at 143°C, being still functional until 250°C, then it slowly degrades till it melts at 343°C. These values help to define the processing temperature and appear to be significantly higher than commonly used plastics like ABS or PET.
- What is the morphology of PEEK?
PEEK is a semi-crystalline material. This means that it is opaque and shows considerable improvements in strength and stiffness, with better high-temperature performances and superior chemical resistance. When cooled too quickly, PEEK can be amorphous, showing translucent-brown areas. Amorphous PEEK has lower mechanical, thermal, and chemical properties. Roboze 3D Printed PEEK has a very high degree of crystallinity, resulting in the best properties possible.
PEEK chemical structure and properties
PEEK offers a unique combination of mechanical properties, resistance to chemicals, wear, fatigue, and creep, as well as exceptionally high temperature resistance. It has also good resistance to combustion and good dielectric performance.
When the applications become more challenging, neat PEEK might still not be resistant enough. To improve its properties, PEEK can be reinforced in different percentages with various elements, like carbon fibers, glass and more. Virgin PEEK is colourless while carbon fiber reinforced PEEK looks black. Both neat and reinforced versions of this polymer are used in a wide range of applications in all industrial sectors.
PEEK material properties table for 3D printing
The main properties of PEEK 3D printed parts are listed in the table below.
Table 1: Technical Data Sheet (TDS) of 3D Printed PEEK by Roboze
Test method | Values | |
---|---|---|
PEEK MECHANICAL PROPERTIES | ||
Tensile Strength (Ultimate) | ASTM D638 | XY 86 MPa - XZ 89 MPa |
Tensile Modulus | ASTM D638 | XY 3.3 GPa - XZ 3.4 GPa |
Flexural Strength | ASTM D790 | 120 MPa |
Flexural Modulus | ASTM D790 | 3.5 GPa |
PEEK THERMAL PROPERTIES | ||
Continuous Use Temperature | ASTM D3045 | 250°c |
Melting Point | ASTM D3418 | 343°c |
HDT @1.82 MPa | ASTM D648 | 150°c |
Glass Transition Temperature | ASTM D3418 | 143°c |
Thermal conductivity | 0.43 W/m*K | |
Lowest temperature | -70°c | |
PEEK PHYSICAL PROPERTIES | ||
Density | ASTM D570 | 1.29 g/cm3 |
Water Absorption | ASTM D792 | <0.45°c |
Moisture Absorption | ASTM D570 | <0.10°c |
UL 94 Flame Class Rating | UL 94 | V0 (@1.5 mm, @1.3 mm) |
Volume Resistivity @23°C | ASTM D257 | 1016 Ohm*cm |
Hardness | ISO 868 | 87 Shore D |
Dielectric constant | 3.2-3.3 (@ 50Hz-10kHz) | |
Coefficient of friction | Low | |
Features | Self-lubricating | |
Colour | Colourless | |
Certifications | NORSOK M710 | |
Resistance to radiation | UV: good |
Physical-chemical properties of PEEK
PEEK belongs to the high-performance polymers. The combination between mechanical strength, high temperature characteristics and superior chemical resistance, make it the material of choice for harsh environments. Let’s check its properties in detail.
- PEEK Mechanical Properties
PEEK has very high mechanical properties, when compared to other thermoplastic polymers. Unreinforced PEEK can reach up to 89 MPa in Ultimate Tensile Strength (UTS), with a tensile modulus of 3.3 GPa. Reinforcing it with Carbon fibers drastically increases its mechanical performance, raising the UTS up to 120 MPa.
Neat PEEK also has a very good flexural behaviour, with a strength till 120 MPa, and a considerable modulus of up to 3,5 GPa.
- PEEK Thermal properties
Although the resistance of plastics at high temperatures is still considered lower when compared to metals, PEEK would make you think again.
PEEK’s melting point is reached at 343°C. Its thermal stability is provided by the ketone group, imparting also high resistance to oxidation. As a result, Polyetheretherketone keeps its mechanical properties unchanged until 150°C (Tg, Glass Transition Temperature) and can be used at temperatures as high as 250°C (Continuous Use Temperature).
Moreover, the low tendency to creep and the good sliding and wear properties are retained over a wide temperature range due to the semi-crystalline nature of this polymer.
- PEEK Physical properties
Maybe one would question about how safe a high temperature polymer would be. Very safe: natural PEEK does not contain any known toxic chemicals and it is inherently flame retardant (UL94 V0) and a low FTS (Flame, Smoke, Toxicity) material. This means that the polymer shows good resistance to combustion and, when it burns, it produces fewer toxic and dense gases than many other high-performance polymers. These features are crucial for safety reasons when it comes to power electronics and transportation applications. PEEK’s excellent thermal and electrical insulation properties make it ideal for electronics applications.
PEEK exhibits only moderate resistance to weathering due to damage caused by UV radiation. β-, ?- and X-rays resistance is very good instead.
PEEK is particularly suitable for tribological application thanks to its very low friction coefficient. Functional Nylon (PA6) and TPU are known to be materials with a low friction coefficient, but the values indicate that PEEK has a better performance.
- PEEK Chemical properties
Do you feel like trying to destroy a PEEK component? That would not be an easy job, since it is known for its excellent chemical resistance to many organic and inorganic chemicals and for its exceptionally good resistance to hydrolysis in hot water.
PEEK is basically insoluble in all common solvents at room temperature, except for some strong acids such as 95% sulphuric acid and hydrofluoric acid.
While PTFE is the only polymer with zero water absorption, there is a broad number of plastics with very low water absorption, like PEEK, PEI (Ultem®), PP, PPS, PSU, PPSU, PVDF, PET, PPE and PE. Among the polymers with a low level of water absorption there are PC, ABS, PA12 and POM.
Thanks to its low water and moisture absorption, the PEEK is often subjected to autoclave processes and can be sterilized.
Unlike other plastics like PP, PC, HDPE, Viton® and Delrin®, it can survive a wide list of aggressive chemicals without any degradation: for example, ozone, peracetic acid (PAA) and ammonium nitrate (NH4NO3).
Do you want to check if PEEK is the perfect material for your application with aggressive chemicals? Check it in the table below!
PEEK Chemical Compatibility Chart
Chart codes
- R - Resistant
- LR - Limited Resistance
- NR - Not Recommended
- ND - No Data
Chemical | Resistance | ||
---|---|---|---|
20°C/68°F | 60°C/140°F | 100°C/212°F | |
Acetone | R | R | R |
Acetylene | R | R | R |
Acid fumes | R | R | R |
Alcohols | R | R | R |
Aliphatic esters | R | R | R |
Ammonia, aqueous | R | R | R |
Aromatic solvents | R | R | R |
Benzene | R | R | R |
Carbonic acid | R | R | R |
Caustic soda & potash | R | R | R |
Chlorobenzene | R | R | R |
Copper salts (most) | R | R | R |
Cyclohexane | R | R | R |
Detergents, synthetic | R | R | R |
Ether | R | R | R |
Fatty acids (>C6) | R | R | R |
Ferric chloride | R | R | R |
Formaldehyde (40%) | R | R | R |
Glycol, ethylene | R | R | R |
Hydrochloric acid (10%) | R | R | R |
Hydrochloric acid (conc.) | R | R | ND |
Hydrocyanic acid | R | R | R |
Hydrofluoric acid | NR | NR | NR |
Hydrogen peroxide (30%) | R | R | R |
Hydrogen peroxide (30 - 90%) | R | R | ND |
Hydrogen sulphide | R | R | R |
Hypochlorites (Na 12-14%) | NR | NR | NR |
Lactic acid (90%) | R | R | R |
Mercury | R | R | R |
Methanol | R | R | R |
Milk products | R | R | R |
Moist air | R | R | R |
Napthalene | R | R | R |
Nickel salts | R | R | R |
Nitric acid (<25%) | R | R | R |
Nitric acid (50%) | R | R | R |
Nitric acid (90%) | NR | NR | NR |
Nitric acid (fuming) | NR | NR | NR |
Oils, diesel | R | R | R |
Oils, essential | R | R | R |
Oils, mineral | R | R | R |
Oils, vegetable and animal | R | R | R |
Ozone | R | R | R |
Phosphoric acid (20%) | R | R | R |
Phosphoric acid (50%) | R | R | R |
Phosphoric acid (95%) | R | R | R |
Sea water | R | R | R |
Silicone fluids | R | R | R |
Silver nitrate | R | R | R |
Sodium carbonate | R | R | R |
Sulphates (Na, K, Mg, Ca) | R | R | R |
Sulphites | R | R | R |
Sulphuric acid (<50%) | R | ND | ND |
Sulphuric acid (70%) | R | R | R |
Sulphuric acid (95%) | NR | NR | NR |
Urea (30%) | R | R | R |
Water, distilled. | R | R | R |
Water, soft | R | R | R |
Water, hard | R | R | R |
PEEK 3D printing Roboze
Thanks to the unique properties of PEEK, feeding a 3D printer with this polymer might be very challenging. The main issue is represented by its high viscosity. Furthermore, high temperatures are necessary to extrude this filament and this creates high thermal stresses when cooling it till room temperature.
Roboze was able to implement PEEK and its composites in its Argo industrial 3D printers, creating specific features on the machines to be fully compliant with the requirements of such a problematic material.
The first implementation on Argo printers is the HVP extruder. This extrusion system was designed by Roboze’s R&D department to reduce friction in the internal channels, enabling the print of high viscosity materials without difficulties.
The second feature is the heated chamber: it assures a homogeneous thermal flow through the whole printing volume, so to have a uniform temperature of 180°C. It ensures a perfect cooling of the filament after the extrusion at 450°C.
Moreover, the heated chamber is a crucial factor for the optimization of the production processes: it reduces the post-production steps, like annealing, reducing costs and times to get the final part. However, this feature alone would not be enough to have a high-quality printed part: precision, accuracy and repeatability are still key factors for Additive Manufacturing to become a success.
This is the reason for the additional characteristics of Argo production systems: the 3d printing Beltless system, the automatic calibration of the Z axis and the automatic build plate leveling.
The high crystallinity level and the outstanding mechanical properties of the 3D printed components pave the way for successful applications.
PEEK Applications: what is PEEK used for?
High mechanical resistance, high temperatures resistance and high chemical inertia: because of its properties, PEEK is used for/to applications in many different industries. Here some examples of PEEK applications:
PEEK for the Energy industry: in environments where different fluids, from fuels to chemicals, are involved, there is room for PEEK to show all the biggest advantages. In the Oil&Gas and Energy industries, PEEK looks like the perfect candidate to resist harsh environments, providing good mechanical properties.
PEEK for Aerospace and Defense industries: thanks to the high performances of PEEK, its use has been widely approved, largely for metal replacement opportunities. Being a polymer with similar properties to metals, it allows for impactful weight saving options that lead to the reduction of consumed fuels and released emissions. Not to mention the flexibility of the production process and the complex geometries that are enabled by Additive Manufacturing.
PEEK for the Transportation industry: the industry connected to the mobility on rails and streets is showing great interest in PEEK, thanks to its abilities to survive in “under the hood” conditions, which means in contact with heat, vibrations, fuels, greases, and dirt. Thanks to its properties, more and more industry sectors are looking at PEEK as a possible way to optimize their processes, increasing the production efficiency.
#PrintStrongLikeMetal #OnDemand