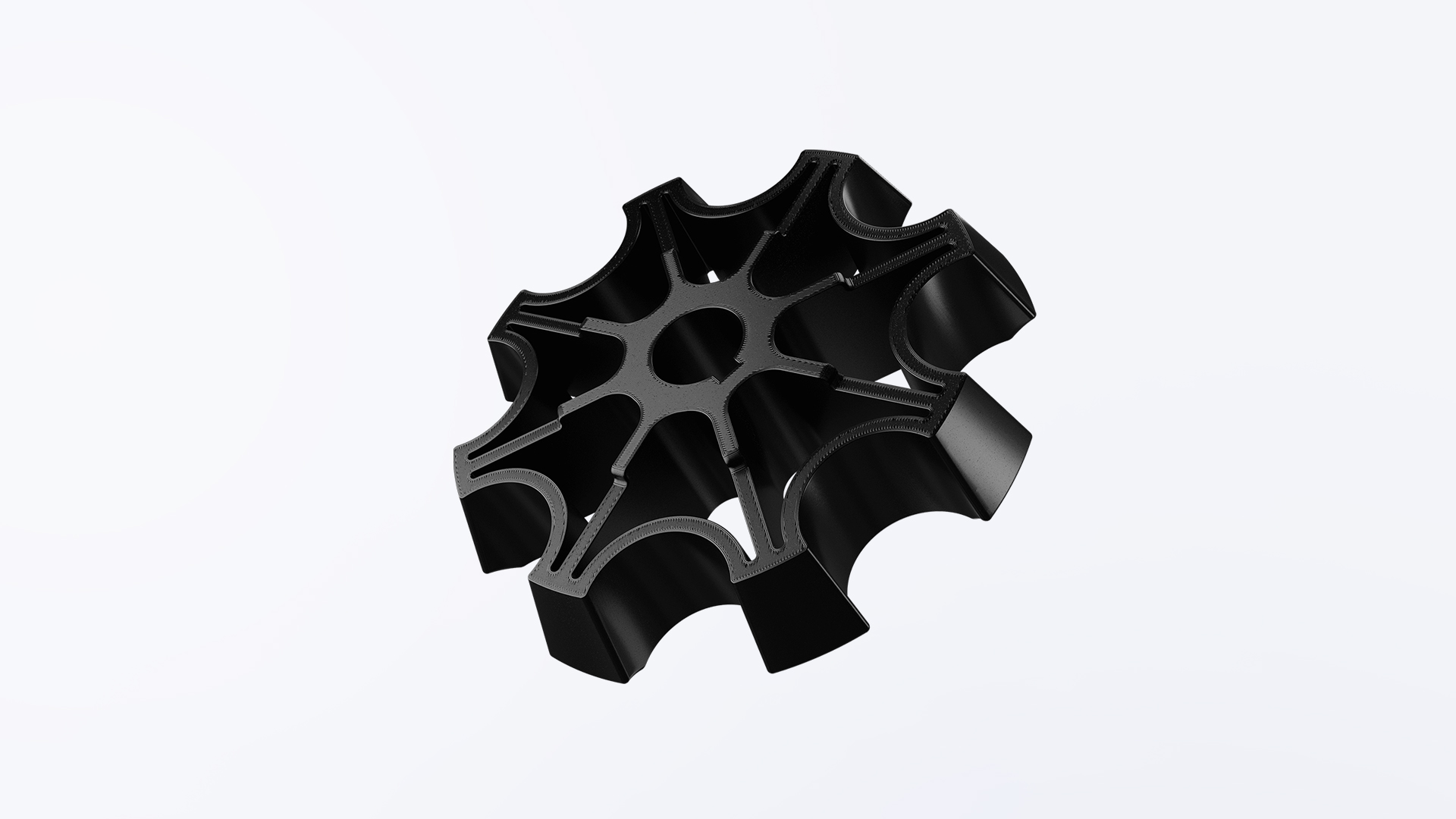
Manufacturing of star wheel conveyors using 3D printing and Roboze Bio-based PA
Star wheels in industrial conveyor systems
Conveyor systems exist in a huge variety of sectors, from food and retail to pharmaceutical to shipping. A major class of components used in these systems are star wheels, which are used to orient and move bottles, boxes, and other types of objects efficiently through mechanical handling systems. These wheels can also be used to divide a stream into two streams having different directions from the starting flow. Another common use is for indexing, where a pre-set number of objects are allowed to continue while the rest are held back until the downstream process is complete.
Which materials do you use to produce star wheels?
Star wheels conveyors are made with a variety of materials including metals such as steel, but depending on the requirements and type of production line they can be manufactured also with plastics such as ultra-high molecular weight polyethylene (UHMW), polyoxymethylene (POM), and polyamide (PA). Typical manufacturing techniques used for their production are casting or CNC machining.
Star wheels come in a huge variety of shapes and sizes according to the role they must fulfil, the objects they need to manipulate, and the line speed. They must be designed to ensure that the objects being handled are manipulated carefully and maintain their integrity in the case of reorientation or movement from one lane to another.
The limits with traditional manufacturing of star wheels
As previously mentioned, star wheels are designed according to the needs of the line they work on. They are also often designed to be interchangeable and removable. When working on production lines that involve objects with complex geometries such as bottles, the star wheels themselves can end up also having very complicated shapes.
It can be difficult for traditional manufacturing techniques such as CNC machining and casting to produce complex shapes, which naturally drives up the cost. This is further compounded by the low production volumes of star wheels, as low as just a few hundred per year.
In production lines that manufacture hundreds of objects per minute star wheels wear down fast, necessitating replacement. Therefore, companies will order a larger amount than they need from external suppliers, both to reduce the cost per wheel and to have spares in stock when needed. The issue here is that storing the spares takes up space that could be employed for other uses, adding to the already high costs.
Roboze 3D printing solutions for star wheel manufacturing
Low production volumes and complex geometries with advanced materials are the main focuses of Roboze’s continuously evolving 3D printing solution ecosystem. The latest addition to the Roboze material portfolio is a Bio-based PA that is strong (66 MPa of tensile strength) and has a low hygroscopicity (0.8% using moisture gravimetric content method). On top of this, it is a 3D printing material composed of components produced from renewable resources and reinforced with natural fibres instead of petroleum-based polyacrylonitrile (PAN) carbon fibres (CFs).
The inclusion of renewable components means that Roboze Bio-based PA has a 60% lower carbon footprint than other comparable filaments. When combined with the outstanding mechanical and hygroscopic properties it enables applications even in production lines that handle fluids while still enabling companies to meet sustainability goals and helps to contribute to a greener future.
The material is manufactured on cutting edge 3D printers that, thanks to Roboze’s patented beltless system, boast the greatest accuracy and repeatability on the market. This leads to the production of very precise parts that can be printed many times with the knowledge that subsequent prints will have the same quality.
Optimisation of a star wheel conveyor for 3D printing with Roboze Bio-based PA
In this application a production line was used to manufacture and package chemicals, some of which were heavily diluted with water. The star wheels in the line needed to manipulate bottle shaped containers of fluid, moving them from one conveyor to an adjacent one. The original part was made from plastic stock using machining, resulting in a heavy wheel that could not be optimised for the manipulation of bottles due to the limitations of traditional manufacturing.
Changes to the production line would necessitate changes to the star wheels, meaning new ones would have to be ordered in large batches to lower the cost per part enough to make it convenient for the factory. The extras needed to be stored and would take up space in the warehouse.
The 3D printed star wheel, shown below, had instead been optimised for the production line thanks to the design freedom of 3D printing. The presence of chemicals and water were not a problem for Roboze Bio-based PA thanks to its nylon matrix and low water absorption rate, giving it several properties such as:
- wide chemical compatibility;
- wear resistance;
- self-lubricating characteristics;
- maintenance of mechanical properties of parts even if there is a spillage.

By lowering the infill, the wheel was made not only lighter but more flexible than material with 100% infill, making it more gentle on the containers but also able to flex slightly and so grip them better. Extra holes had also been included to further lighten the wheel, with CNC machining the material removed would have been wasted.
By having a digital model of the wheel and an in-house printer, the factory was able to print the part on-demand and just-in-time without needing to order and store spares. On top of that, modifications to the star wheels were easily implemented when the line changed, allowing the factory to optimise the production lines for the products instead of around the limitations of star wheel manufacturing.
Material | Nylon 6, CNC machining | Roboze Bio-based PA, 3D printing |
---|---|---|
Material waste | 79% | 3% |
Weight of final part | 0.372 kg | 0.367 kg |
Manufacturing time | 13 days | 10 hours |