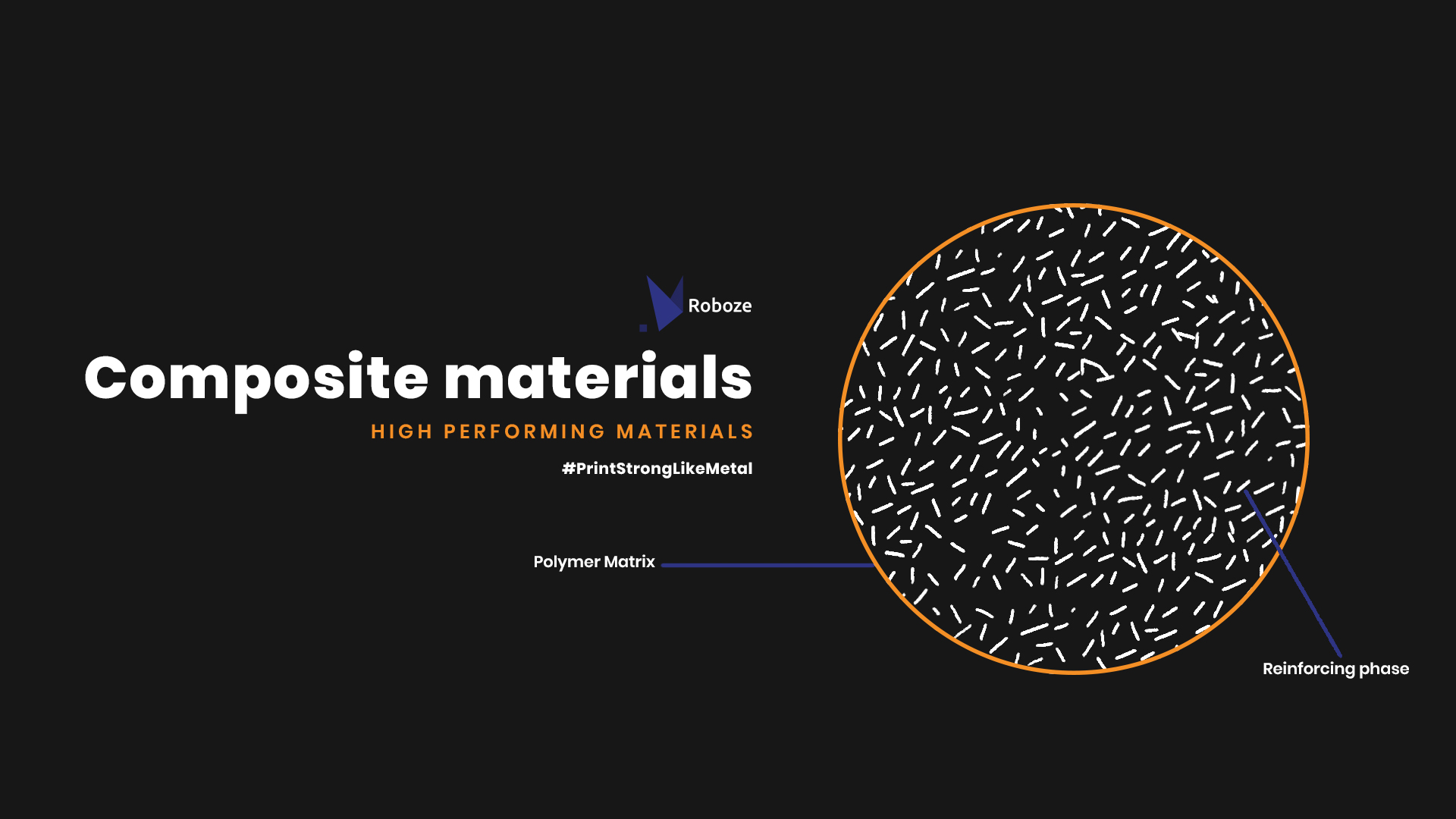
High performance materials: the composite materials
In recent years, the use of composite materials in additive manufacturing has seen significant evolution, thanks to the innovative solutions developed by Roboze. Composites, known for their high mechanical and thermal resistance, are unlocking new possibilities in strategic sectors such as energy, mobility, and aerospace. Roboze, with its advanced printing technologies like the ARGO 1000 HYPERMELT and ARGO 500 HYPERSPEED, has revolutionized component production, offering advantages in terms of speed, precision, and material quality.
Roboze Solutions: ARGO 1000 HYPERMELT and ARGO 500 HYPERSPEED
Roboze technologies stand out for their unparalleled performance in the additive manufacturing of composite materials. The ARGO 1000 HYPERMELT is designed to produce large composite parts, up to 1m³, with superior quality and precision compared to existing pellet-based systems. It leverages an advanced melting process to improve print speed, material mechanical properties, and surface resolution at the same time. The ARGO 500 HYPERSPEED, on the other hand, is ideal for the rapid production of small-to-medium-sized composite parts, combining speed and precision without compromising on quality, making it perfect for industrial applications where time-to-market is critical.
Roboze Composite Materials
Roboze offers a range of high-performance composite materials, optimized to tackle the most complex challenges in industrial sectors. These materials are designed to ensure strength, lightness, and durability, even in extreme conditions:
• Carbon PEEK: Carbon PEEK is a composite reinforced with 20% carbon fiber, which increases strength, stiffness, and load-bearing capacity compared to pure PEEK. With its enhanced thermal and electrical conductivity and chemical resistance, it is ideal for metal replacement in extreme environments such as aerospace, oil & gas, and motorsport. It is certified for the railway sector.
• Carbon PA PRO: Carbon PA PRO is a carbon fiber-reinforced polyamide with a tensile strength of 171 MPa, making it one of Roboze's strongest materials. It is ideal for high mechanical stress applications, such as structural components in motorsport, drone frames, and production tooling.
• ToolingX CF: ToolingX CF is a semi-crystalline PPS-based composite reinforced with carbon fiber. It is highly resistant to high temperatures and chemicals, making it ideal for producing tooling such as thermoforming molds. It is also certified for the railway sector and has ESD properties, making it suitable for sensitive electronic components.
• MATRIX: MATRIX is a PA-based composite reinforced with 15% chopped carbon fibers, known for its excellent surface resolution. While less strong than Carbon PA PRO, it is ideal for applications requiring high aesthetic quality and dimensional precision, such as control jigs, brackets, sliding guides, and welding masks. It is perfect for projects requiring optimal surface finish and ease of machining.
Applications in Strategic Sectors
Roboze's composite materials are applied across various industrial sectors, addressing challenges in traditional manufacturing and delivering significant benefits in terms of efficiency and performance:
• Energy: Due to their resistance to extreme environmental conditions, Roboze composites are ideal for components used in energy plants, ensuring durability and reliability.
• Mobility and Transportation: In the railway and automotive sectors, composites help reduce vehicle weight, improving energy efficiency and lowering operational costs.
• Aerospace: The ability to maintain high performance even in extreme conditions makes these materials perfect for aerospace applications, where weight reduction and reliability are critical.
Success Stories: Examples of Applications with Roboze
Roboze has demonstrated its impact across multiple sectors, thanks to its ability to produce high-performance components using advanced composite materials. Here are some real examples of how our technology has transformed manufacturing in various contexts.
• Aerodynamic Components in Racing: In the world of motorsport, the use of additive manufacturing with composite materials like Carbon PA PRO has enabled the development of aerodynamic components that significantly improve on-track performance. These components, characterized by their lightness and mechanical strength, help optimize airflow and reduce the overall weight of the vehicle. Learn more about how we enhanced aerodynamic performance with Roboze technology. Download the full document here.
• Swing Check Valves Trim – Metal Replacement: In the industrial sector, oscillating check valves produced with Carbon PEEK represent a revolution in metal replacement. Thanks to Roboze solutions, these components not only offer performance comparable to metals but also significantly reduce weight and production times, while increasing chemical resistance. Learn more about the advantages of metal replacement with Roboze. Download the full document here.
• Production of Thermoforming Molds for Plastic Tubes: Roboze has contributed to improving the production of molds for plastic pipe thermoforming with the use of ToolingX CF material. Its excellent thermal stability and mechanical properties make it an ideal candidate for high-temperature environments, reducing production times and improving mold durability. Discover how Roboze optimized the production of thermoforming molds. Download the full case study here.
Want to learn how Roboze can optimize your production with advanced composite materials? Contact our experts and start turning your ideas into reality with solutions tailored to your industrial needs. We are ready to support you every step of the way.