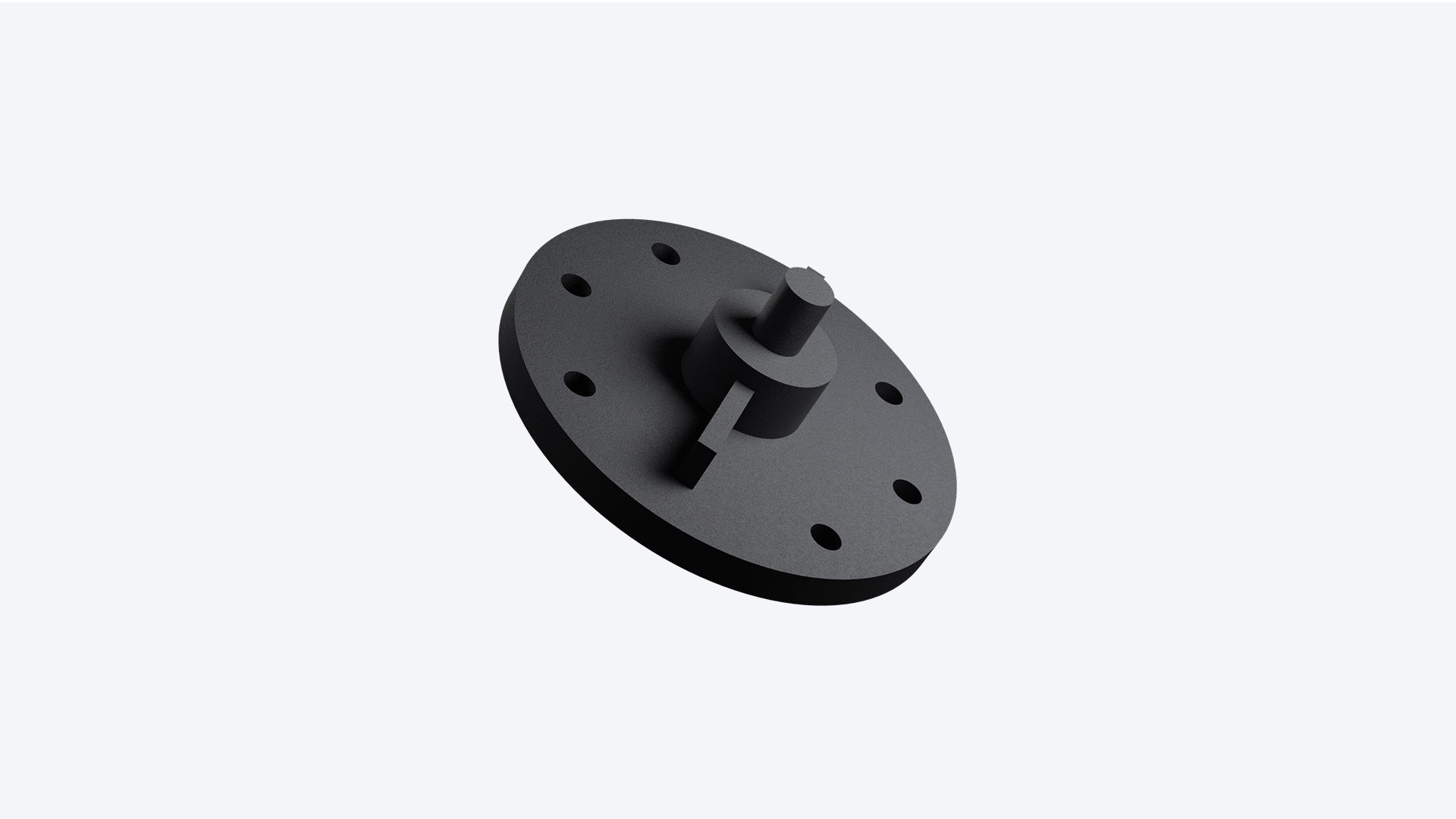
Custom Additive Manufacturing of Industrial Equipment
Today’s manufacturing companies are constantly looking for ways to reduce costs, increase precision, and speed up production. Additive manufacturing of custom industrial equipment is a powerful solution that helps achieve these goals. But how exactly does it work, and what advantages can it offer to your business?
What is Additive Manufacturing of Industrial Equipment?
Additive manufacturing, often called 3D printing, enables the production of custom industrial equipment directly from digital models. This technology significantly reduces prototyping and production times compared to traditional methods like milling or molding. At Roboze, we specialize in industrial 3D printing, offering the design and production of precision tools and custom components tailored to meet the specific requirements of your production line.
Benefits of Additive Manufacturing for Industrial Equipment
Why should companies consider additive manufacturing over traditional methods for industrial equipment manufacturing? Here are some key benefits:
• Reduced Production Times: With additive manufacturing, you can produce metalworking tools and other technical instruments in much shorter timeframes than with conventional processes.
• Extreme Customization: Each tool or component can be custom-designed for your specific needs, such as custom tooling for assembly lines or specialized injection molding tooling.
• Cost Reduction: 3D printing eliminates the need for expensive molds or tooling, significantly lowering overall manufacturing costs.
When to Choose Additive Manufacturing Over Traditional Methods?
Many businesses are evaluating the switch to additive manufacturing for certain types of industrial production machinery. This technology is especially advantageous for small series or highly customized production runs. 3D printing enables fast production of injection molding tooling and custom components, making it perfect for on-demand manufacturing or specialized projects that demand high flexibility.
Another context in which additive manufacturing is extremely effective is in reducing downtime. Additive manufacturing can quickly produce industrial maintenance equipment, which minimizes operational downtime and improves the continuity of your production processes. This capability ensures you can maintain high levels of efficiency and productivity across your entire operation.
Common Applications of Additive Manufacturing in Industrial Equipment
The application of additive manufacturing spans a variety of industries and use cases. Below are some of the most common:
• High-Precision Machining Tools: These tools are used in industries where precision and control over tolerances are critical.
• Quality Control Tools for Production Lines: With 3D printing, you can create custom tools that optimize monitoring and verification during production, ensuring consistent quality.
• Custom Tooling for Assembly Lines: Building tools specifically for your assembly processes ensures seamless integration with the rest of your production machinery.
Roboze: Your Partner for Additive Manufacturing of Custom Equipment
If you’re seeking to increase flexibility and improve production efficiency, additive manufacturing is a key solution. Roboze offers advanced, customized industrial 3D printing solutions that meet the demands of various sectors, including automotive, motorsports, and aerospace. Our technology allows you to achieve durable, precise, and customized results tailored to your specific production needs.
How to Get Started with Additive Manufacturing?
Thinking about implementing additive manufacturing in your business? Contact our team of experts today to learn how Roboze can help you streamline your production processes, reduce costs, and enhance precision.