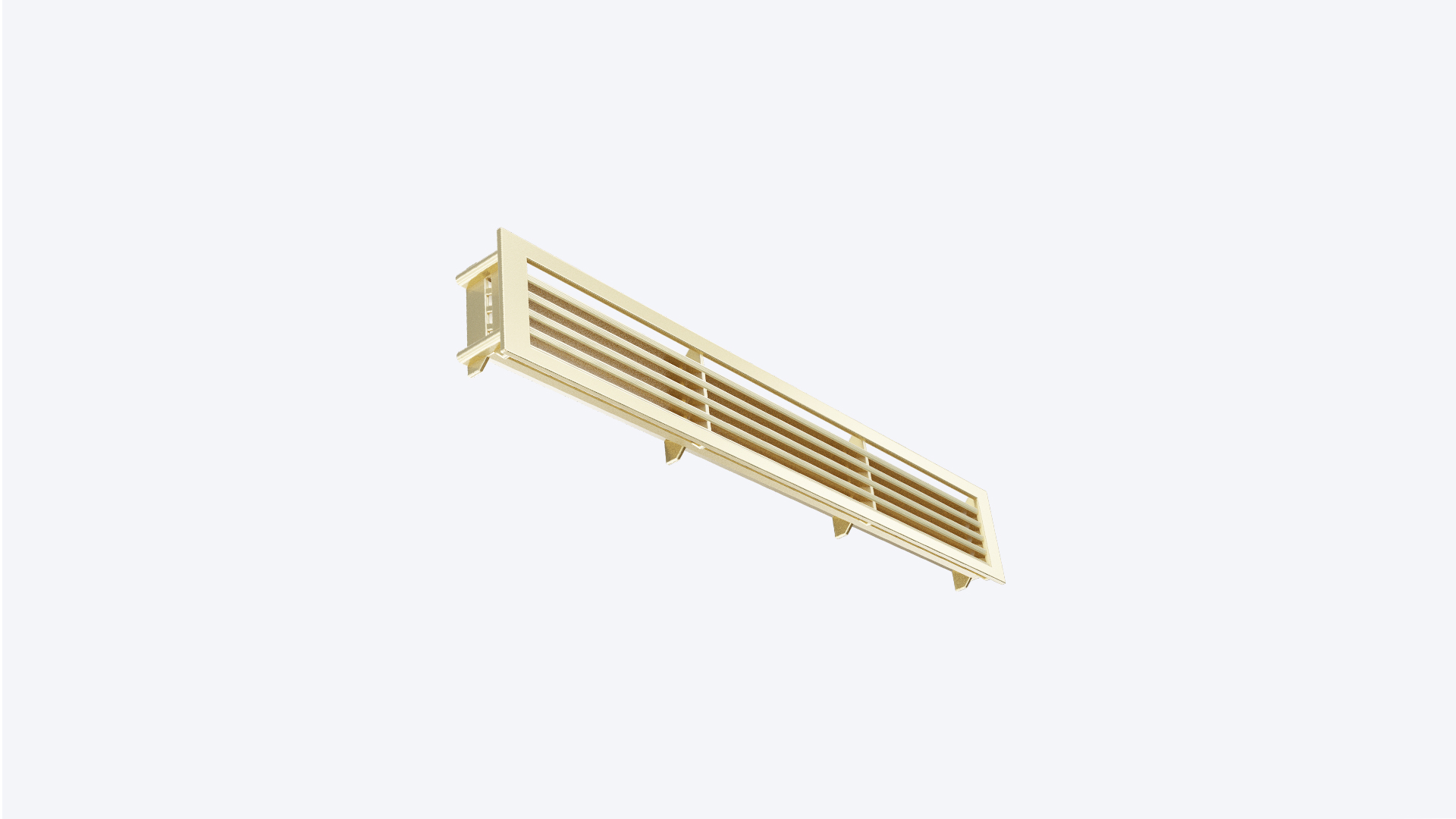
Additive manufacturing of ventilation grilles in ULTEM™ AM9085F in the railway industry
The ECS (Environment Control System) represents the beating heart of comfort inside trains, ensuring a pleasant environment for passengers thanks to the regulation of temperature and ventilation. In this context, ventilation grills emerge as crucial components, playing a decisive role in allowing the controlled passage of treated air. These elements, however, not only contribute to the well-being of travelers but also face significant challenges during the production process.
The ventilation grills, therefore, represent the link between the ECS system and the passengers, being the only element in direct contact with those who use the transport service. This privileged position, despite being of fundamental importance, often exposes them to damage and requires periodic maintenance, as they are visible and susceptible to wear.
Furthermore, the production of ventilation grilles often involves welding processes, presenting significant challenges in terms of quality control. Precision becomes crucial to avoid unwanted leaks that could compromise the overall efficiency of the ECS system. The need to ensure precise welding adds complexity to the production process, requiring a particularly high level of attention and expertise. The welding process, although essential, represents one of the most critical stages in the production of ventilation grilles. The challenge lies in the need to balance the strength of the welds with the precision required to avoid air leaks. Furthermore, the use of lightweight materials, which is common in modern ventilation grilles, adds further complexity to welding, requiring specialized skills to ensure structural strength without compromising the desired lightness.
The Roboze solution: ARGO 500 and the ULTEM™ AM9085F material
The adoption of additive manufacturing with Roboze systems and the use of ULTEM™ AM9085F material offers unprecedented flexibility, allowing the creation of complex, customized geometries with millimeter precision. This versatility reduces production times and overall costs.
The main advantages compared to traditional methods are:
• No welding required: Roboze's additive approach eliminates the need for welding, simplifying the manufacturing process and mitigating the risks of structural defects.
• Digital warehouse: Additive manufacturing enables the creation of a "digital warehouse", simplifying the management of ventilation grille projects. This not only reduces the costs associated with managing the physical warehouse but also facilitates the reproduction of components when necessary.
• Railway Certified: ULTEM™ AM9085F material complies with railway standards, ensuring that the ventilation grilles meet rigorous safety and quality regulations in the railway industry.
In conclusion, the adoption of additive manufacturing with Roboze systems and the use of ULTEM™ AM9085F material represents a significant advancement in the rail industry. This innovation improves efficiency and precision in the production of ventilation grilles, reducing overall costs and ensuring high safety and quality standards.
To find out more, don't hesitate to contact us!