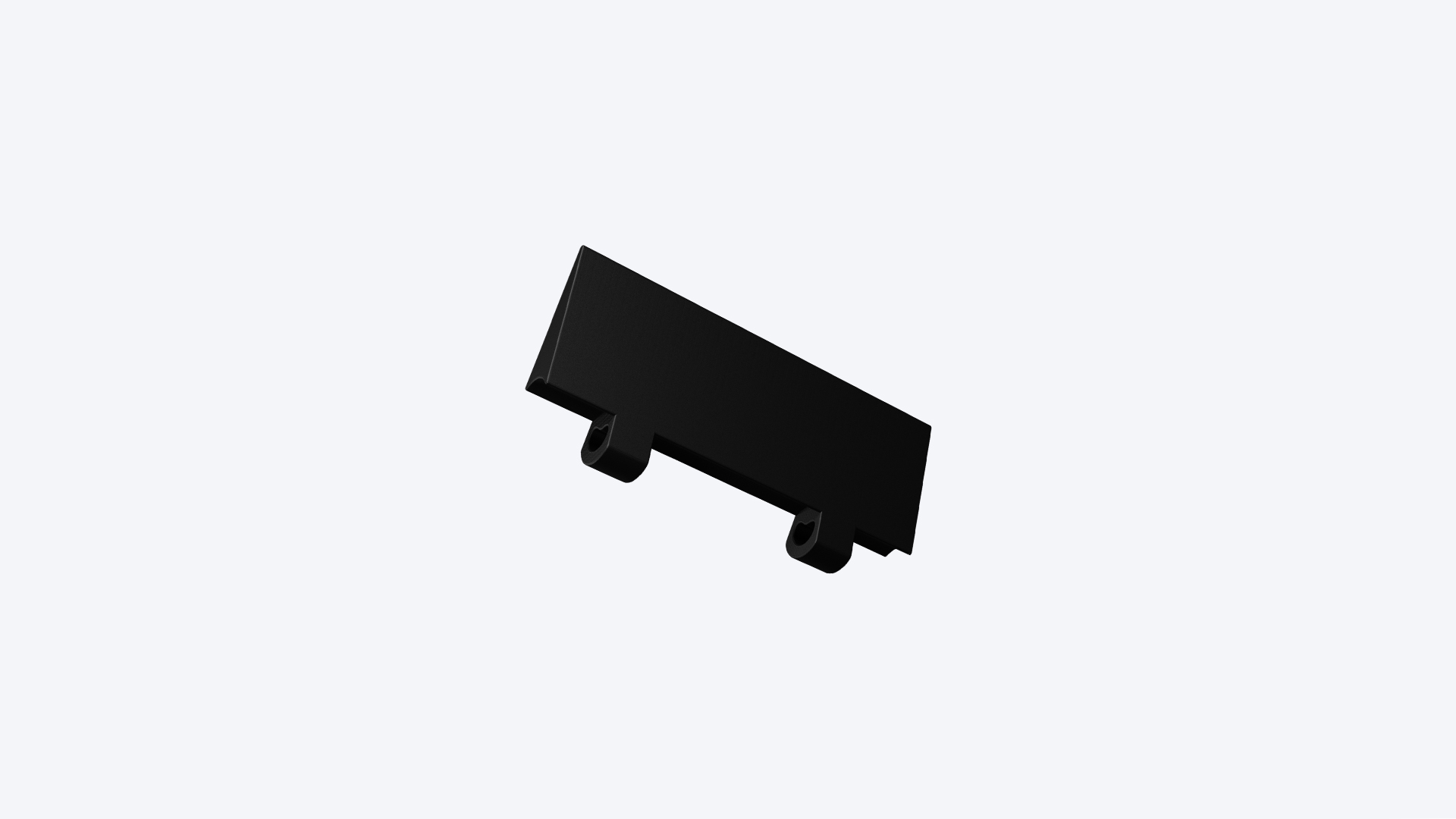
In the constant evolution of the UAV (Unmanned Aerial Vehicle) sector, the design and production of critical components such as the rudder require an innovative approach to guarantee lightness, resistance and customization. By exploring the challenges of traditional manufacturing and the benefits of 3D printing with advanced materials, a solution emerges that revolutionizes the landscape of the aerospace industry.
UAVs represent a cornerstone in aerial operations, offering flexibility and access to previously inaccessible areas. The rudder, essential for direction control, requires optimized design and manufacturing to ensure stability and maneuverability. 3D printing with advanced materials, Roboze ARGO 500 and CARBON PA PRO, offers an innovative solution to overcome the limitations of conventional methods.
Traditional rudder manufacturing methods, in fact, present significant challenges, from the inefficiency in creating complex geometries to the limited choice of lightweight materials. Machining, injection molding and manual lamination of composite materials can hinder the flexibility and customization needed to adapt to the changing needs of the UAV industry. These processes, in addition to requiring long production times, can compromise the strength and structural integrity of the rudder.
With Roboze's 3D printing technology, it is possible to obtain light but robust rudders, customized for specific needs. This allows improving the performance of UAVs, reducing production times and ensuring greater flexibility in the design process.