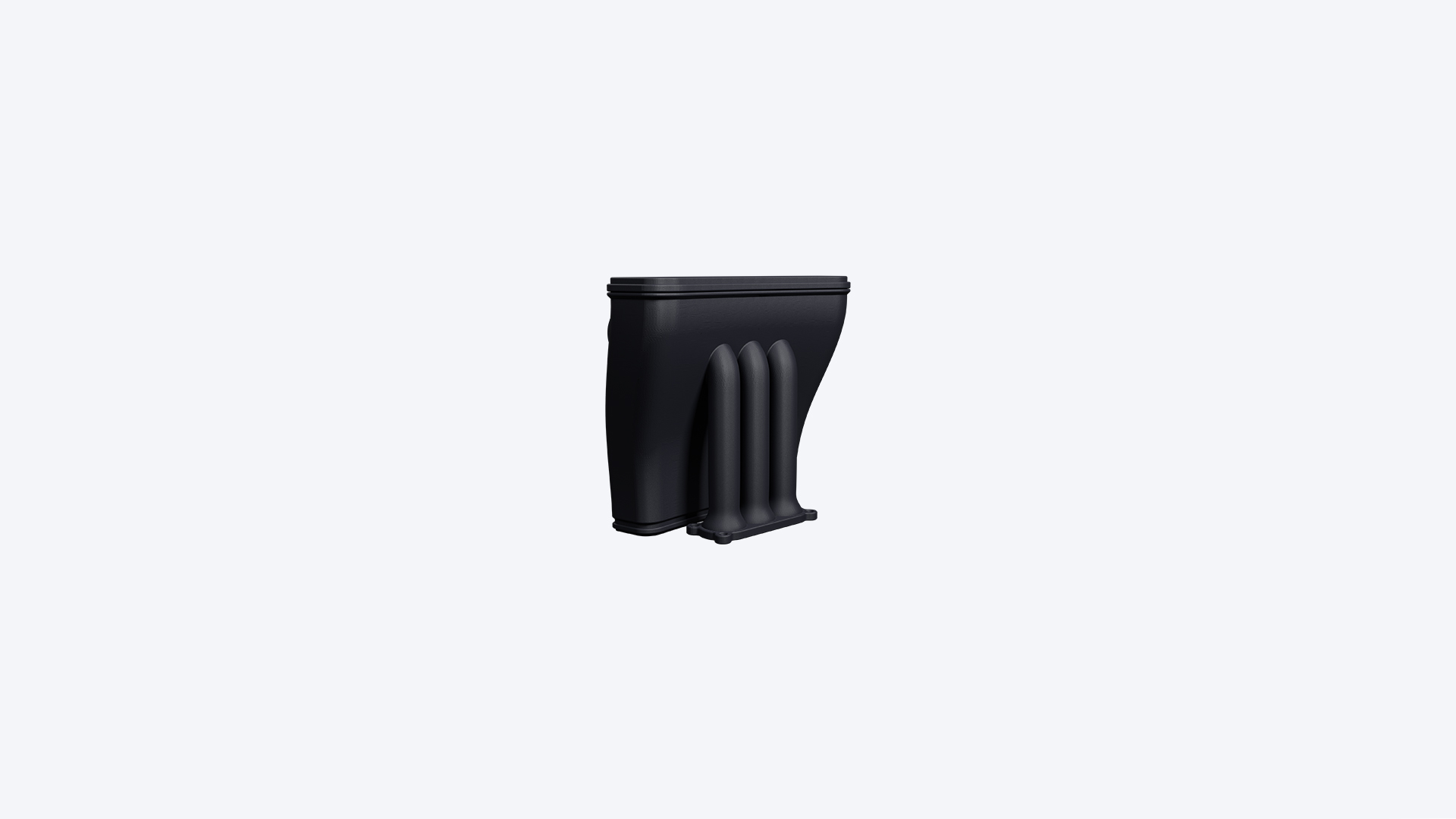
In the world of motor racing, innovation is the key to achieving top-level performance. A customer active in this sector has revolutionized the production of the cooling duct of the braking system of his racing vehicle, adopting the ARGO 500 industrial 3D printer and the CARBON PEEK composite material. This choice has led to significant advantages in terms of production times and design freedom.
The cooling ducts of the braking system in racing vehicles are essential for dissipating the heat generated by braking. The use of advanced technologies such as industrial 3D printing and high-performance materials allows for a more flexible design, improving the overall performance of the braking system.
Traditional manufacturing of brake system cooling ducts often involves complex processes such as lamination of carbon fiber with dissolvable mandrels and the use of bonding. These methods can be effective but have some key limitations, including significant geometric restrictions and additional complexity in manufacturing time.
The use of the ARGO 500 industrial 3D printer and the CARBON PEEK composite material allowed to reduce production times, obtain greater design freedom and improve the overall performance of the racing vehicle.